Utilizing Thermex-Thermatron’s RF Tooling Expertise
Thermex-Thermatron Systems
When welding flexible materials with a radio frequency (RF) heat sealing machine, advanced tooling is imperative. Consider that any results of high frequency welding will hinge upon the RF tooling used to carry out production. Tackling the fabrication of large products with the wrong welding tooling will come at a steep cost. Conversely, applying proper RF tooling allows you to secure a durable weld, safe to withstand storms — all while still honoring aesthetic design.
For decades now, Thermex-Thermatron Systems (“Thermex”) has pioneered and shaped the development of premier radio frequency and microwave (MW) equipment. With over 80 years of technical expertise, Thermex’s skilled and qualified team understands the ins and outs of RF heat sealing to RF tooling; from design through engineering and manufacturing. Leveraging top insights, gathered from firsthand experience while working with industries across the globe, Thermex’s leading RF, MW, and industrial technology has empowered manufacturers to make production safer and more efficient — all while delivering the utmost quality.
Harnessing properly designed tools will make a transformative difference in the outcome of lifesaving products; and when the ability to achieve (and repeat) accuracy is paramount, operating consistent, intelligently designed equipment is essential. Combining Thermex-Thermatron’s customizable RF tooling services (also called RF heat sealing dies) with the Thermatron line of heat sealers, manufacturers rely on intricate RF tooling able to satisfy the complexities of products and processes alike; without compromising on standards.
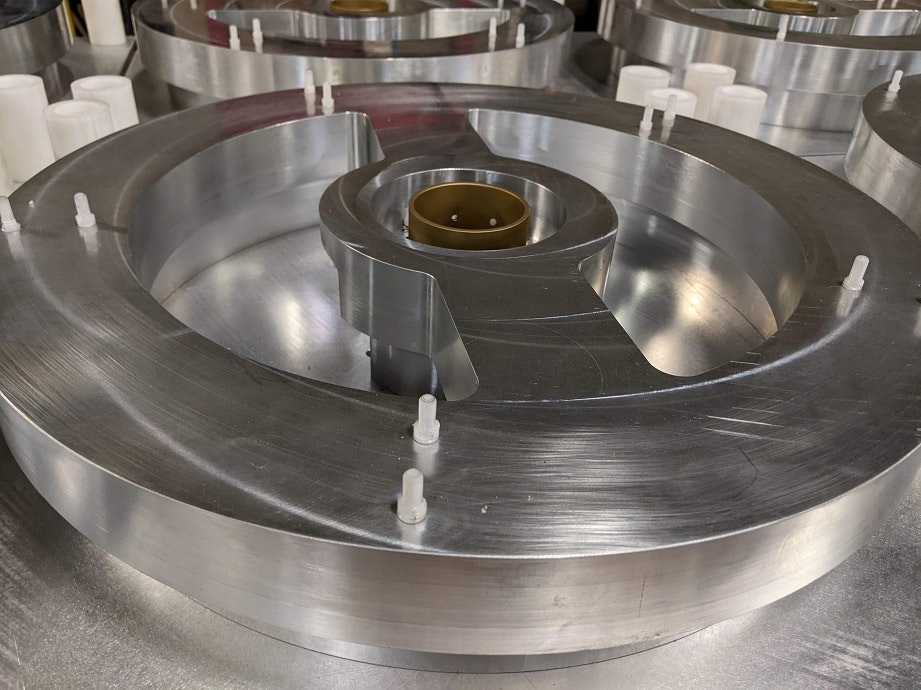
The Many Shapes and Sizes of RF Welding Tools: Modern Versatility to Meet Industry Demands
In addition to being known as dies, RF welding tools are referred to as electrodes, molds, and fixtures, as well as welding bars. Engineered in all shapes and sizes, the design of these tools is contingent upon differing product requirements along with the available electromagnetic field (created by the RF generator). For instance, to match a specific product appearance, RF tools can be tailored with different surface finishes.
Typically, RF tooling is made from aluminum or brass in a rectangular or cube-shaped cross section; and mounted to the tool holder of a stationary or traveling welder. While brass dies are more expensive, they ensure durability; and for any maintenance needed, are much easier to repair. In turn, aluminum dies are a lower cost alternative; easier to fabricate and to change. Moreover, in aluminum form, dies offer greater longevity — lasting longer, because aluminum won’t compress or “mushroom out” over time.
Often found on equipment like Thermatron Bar Welders or FIAB Traveling RF Welders, manufacturers leverage welding bars alongside these powerful RF Systems to create large products. Meaningfully cutting down on material handling time, Traveling Welders, optimizing specialized tools, serve the mass assembly of sizable goods — accelerating efficient and economical production processes.
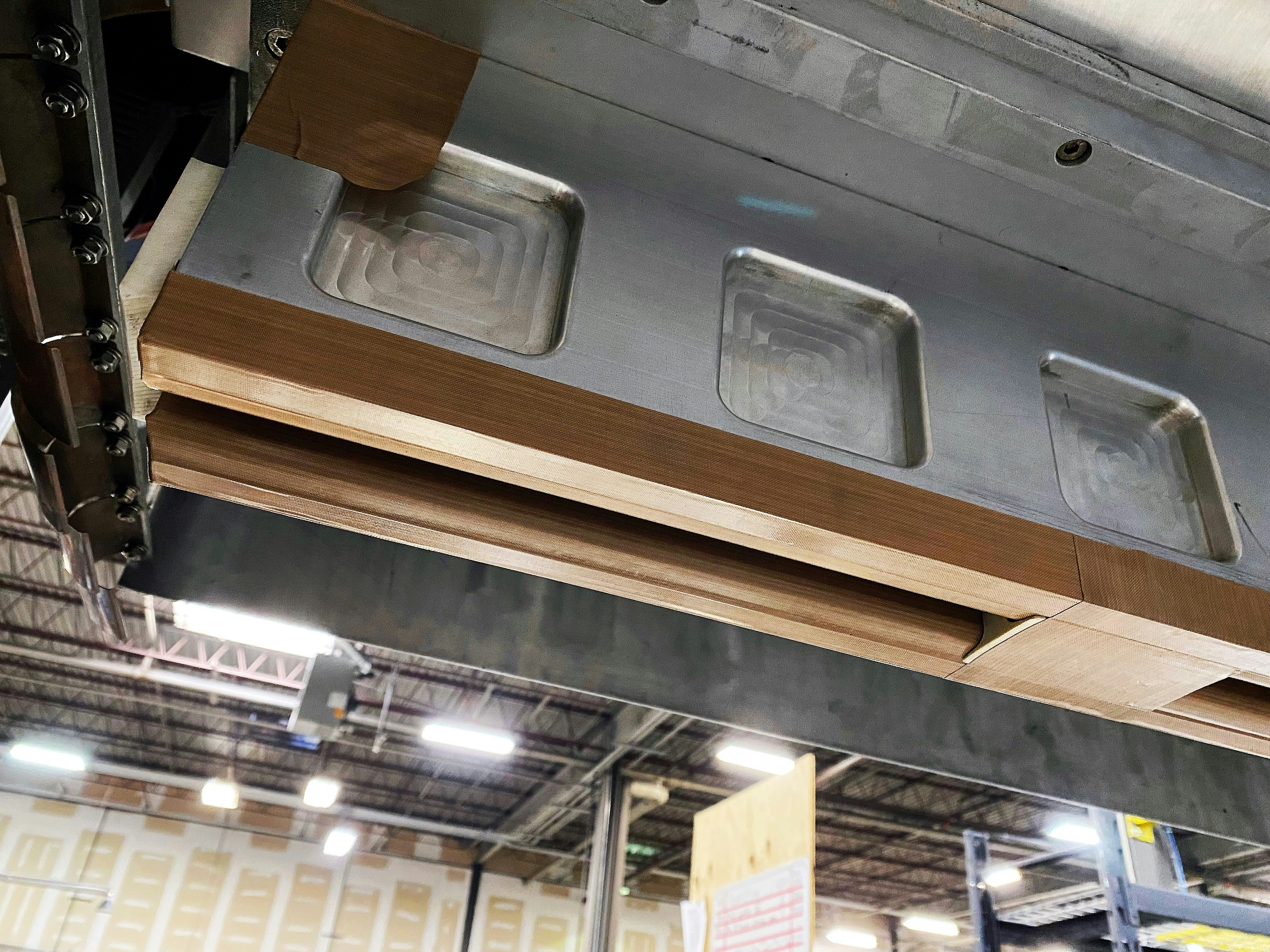
Special cleat mold mounted in a Thermatron RF Press
Drawing on “Soft” Tools to Ensure Storm-Resistant Welds
Consider that the screen products industry calls for welds to be not only resilient, but also elegantly made. This is where “soft” tools come in, seeing to it that welds can be both impenetrable and aesthetically sound. Soft tools are covered in a special foam that presses the materials together when they are not perfectly even; for instance, the mesh materials used in the screen industry. This guarantees edges will be bonded fully to the mesh — thereby securing a stronger weld.
When implementing the welding process, the type of materials as well as the design of the bar used will determine two crucial outcomes: the quality of the weld and the life span of your materials. Using the right materials and applying the best possible design with a highly engineered bar will not only uplevel the quality of your weld, but likewise will heighten the endurance and performance of your materials. Innovating cutting-edge technology and building high-powered equipment capable of replicating precise, streamlined results, Thermex-Thermatron has fostered the expertise to produce exceptional tools, fixtures, and guides, allowing manufacturers to quickly meet top industry standards for these applications.
RF Tooling (left to right) – RF Tooling Bar, RF Soft Bar, RF Slinky Bar
How RF Welds Are Made
- The weld is created by the capacitive load of the tool.
- The capacitive load causes the bi-polar molecules (typically found in PVC and PU materials, among others) to oscillate, heat up, and form a bond under pressure once cooled.
- This bond is now all one material — where the molecules are blended together under pressure, generating their own heat from the electromagnetic field.
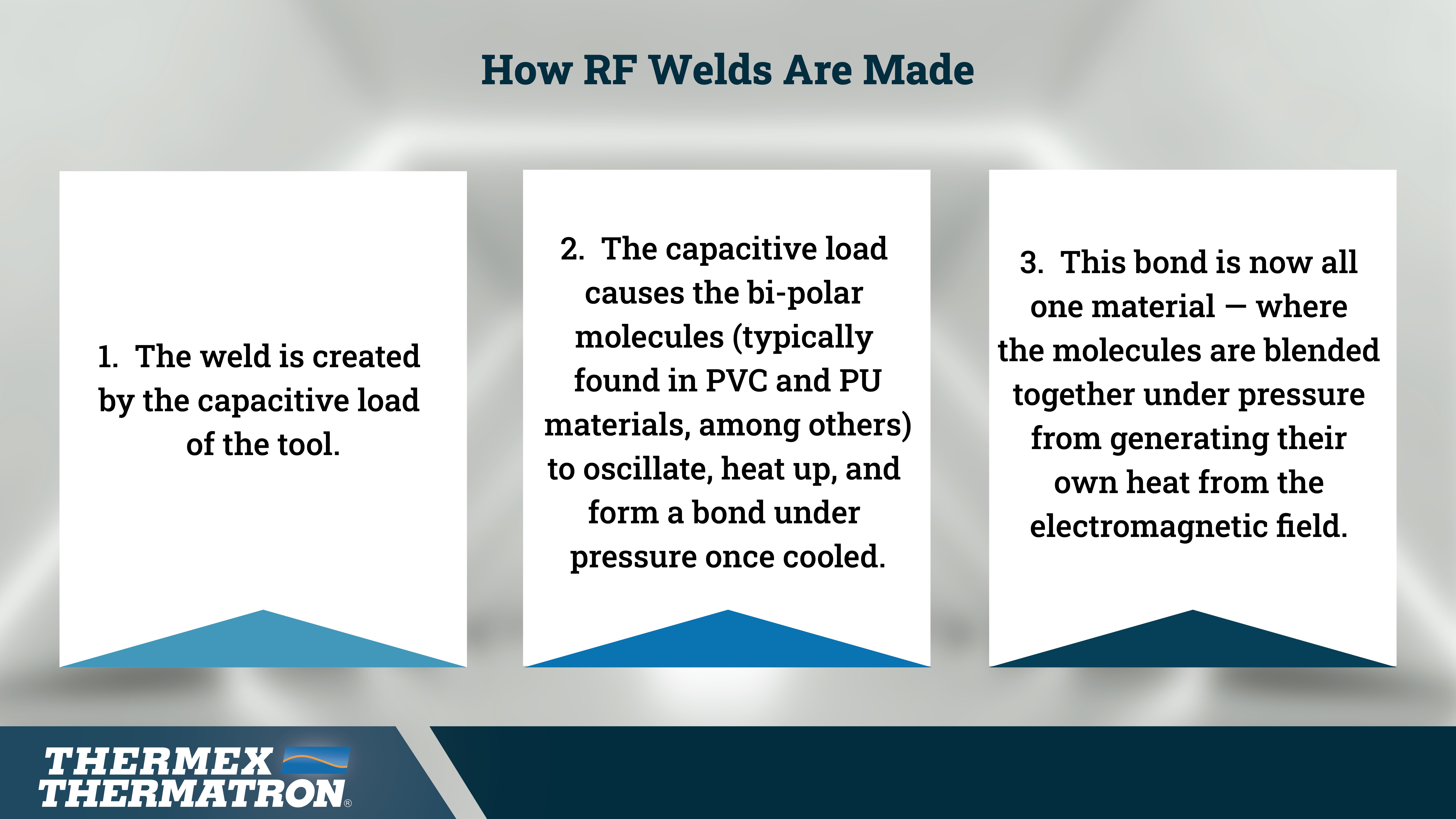
The welding process for larger products presents unique challenges, which is where the knowledge of welding needs and the proper technology to navigate those complex needs become indispensable. Notably, structures, tents, tarps, and straps are made of much thicker materials. When welding over joint or reinforcement patches, consider that those varied thicknesses will not allow a standard bar to evenly weld across the different layers.
One of the top ways to boost productivity: using a “Slinky” bar; a highly developed tool that Thermatron manufactures in-house. This will deliver a reliable, full weld, utilizing even pressure over different steps — the difference when straps and multiple thicknesses are able to be welded with just one hit. Optimizing maximum efficiency, this RF tooling method curbs several steps, saving manufacturers a significant amount of production time; all while minimizing the risk of potential failures in the field.
Harnessing RF technology, factories can adeptly and swiftly weld materials, no matter their differing levels of thickness. However, without a slinky tool, multiple welds with alternate settings are required to be able to weld assorted material thicknesses. Moreover, these additional hits then increase the pitfalls of accidentally using the wrong setting or incorrect alignment — both of which jeopardize the ability to ensure a complete seal.
Why Conveyor Belt and Medical Industries Are Switching to RF Welding
As more and more manufacturers begin to switch to RF welded cleats, demand for well-designed tooling to construct lightweight conveyor belt cleats and splices continues to rise. Market growth here is driven by two key factors:
- The need for void-free welds on food grade belts.
- Lack of need for trimming on PVC cleats.
With the industry calling for sharper quality, the ability to provide precise, custom tooling is more critical than ever; giving manufacturers the dedicated resources they need to produce high-caliber belts.
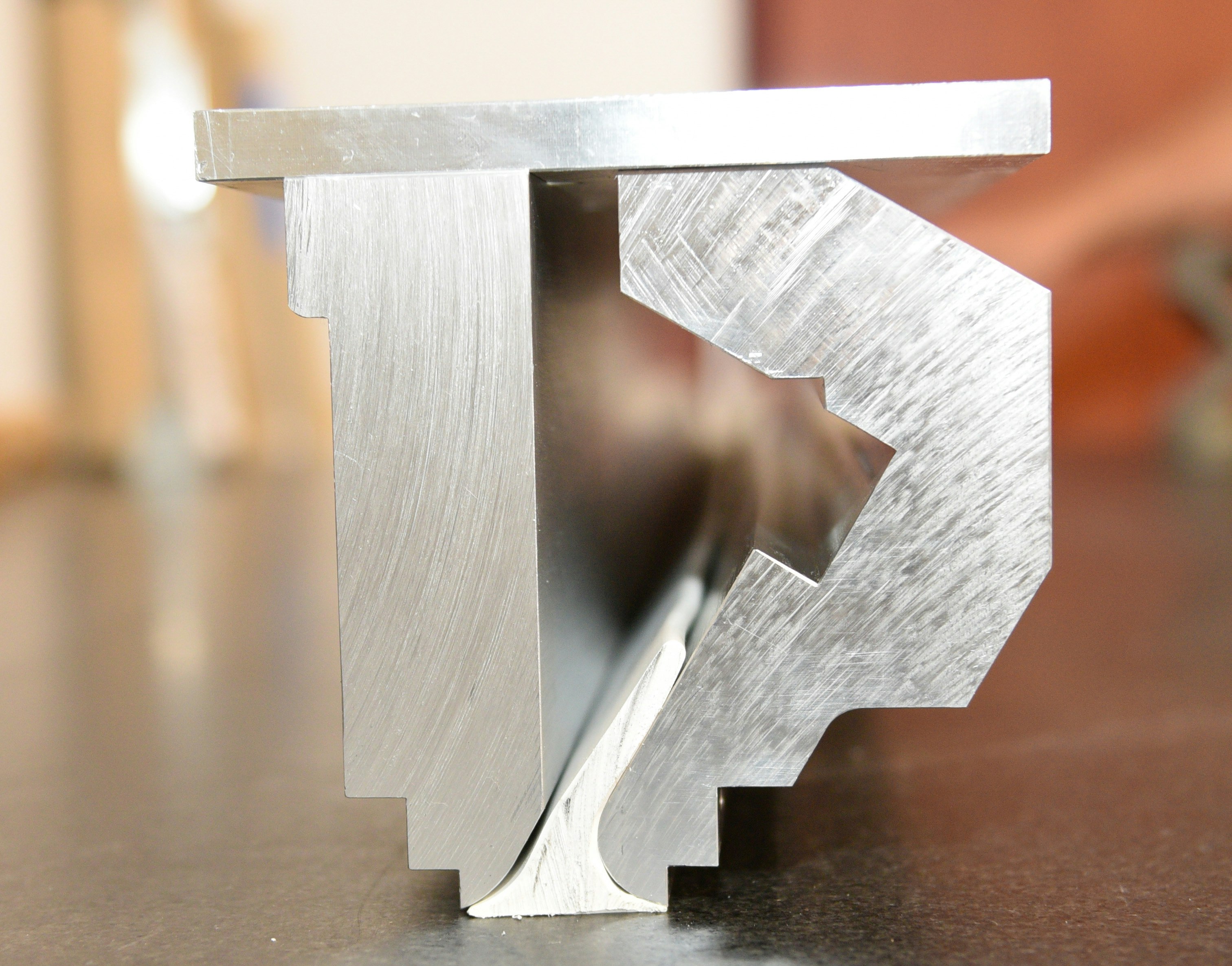
Thermex-Thermatron engineers are experts in the design and application of RF technology — applying this craftsmanship to sophisticated tooling design that empowers manufacturers to produce high-quality end products. With advanced CNC machines and vast experience across the industry, Thermex is skilled and qualified to produce tools for almost any shape of cleat or finger splice; and has designed labor-saving tools for scoop cleats to angled cleats.
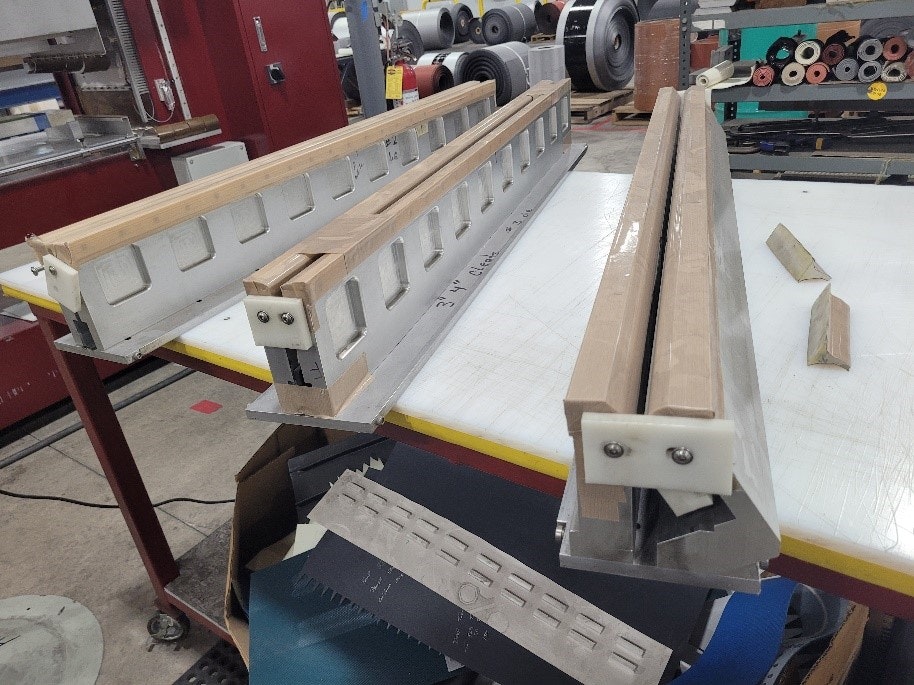
Sample RF Cleat Tooling for three different types of cleats used in the Conveyor Belt Industry

Sample RF Welded Conveyor Belt Cleat
When assessing the intricacies of RF tools, medical products tooling can be the most complex of all. This is an industry where top-of-the-line tools, well-suited for rising demand in a post-COVID-19 era, are integral, affecting the integrity and reliability of a given weld on all types of products. Consider that every blood bag made, every collection bag, irrigation bag, IV bag, and pressure cuff, down to each piece of bio-process containment is only as strong as its weakest weld; and a poorly made weld will wreak detrimental consequences with grave stakes — where hazardous medical care could leave lives in peril. As such, the design and fabrication of these tools require deep understanding of how materials flow around tubes and fittings, among other pressing, nuanced considerations.
When welding tubes, equipment featuring a built-in RF Switching Network is a fundamental asset on the production floor. First, RF technology will direct to a mandrel inside the tube. Simultaneously, the top and bottom tools are grounded. Then, RF technology will switch to the top tool, where the mandrel will be neutral; allowing the material to be fully welded around the tube.
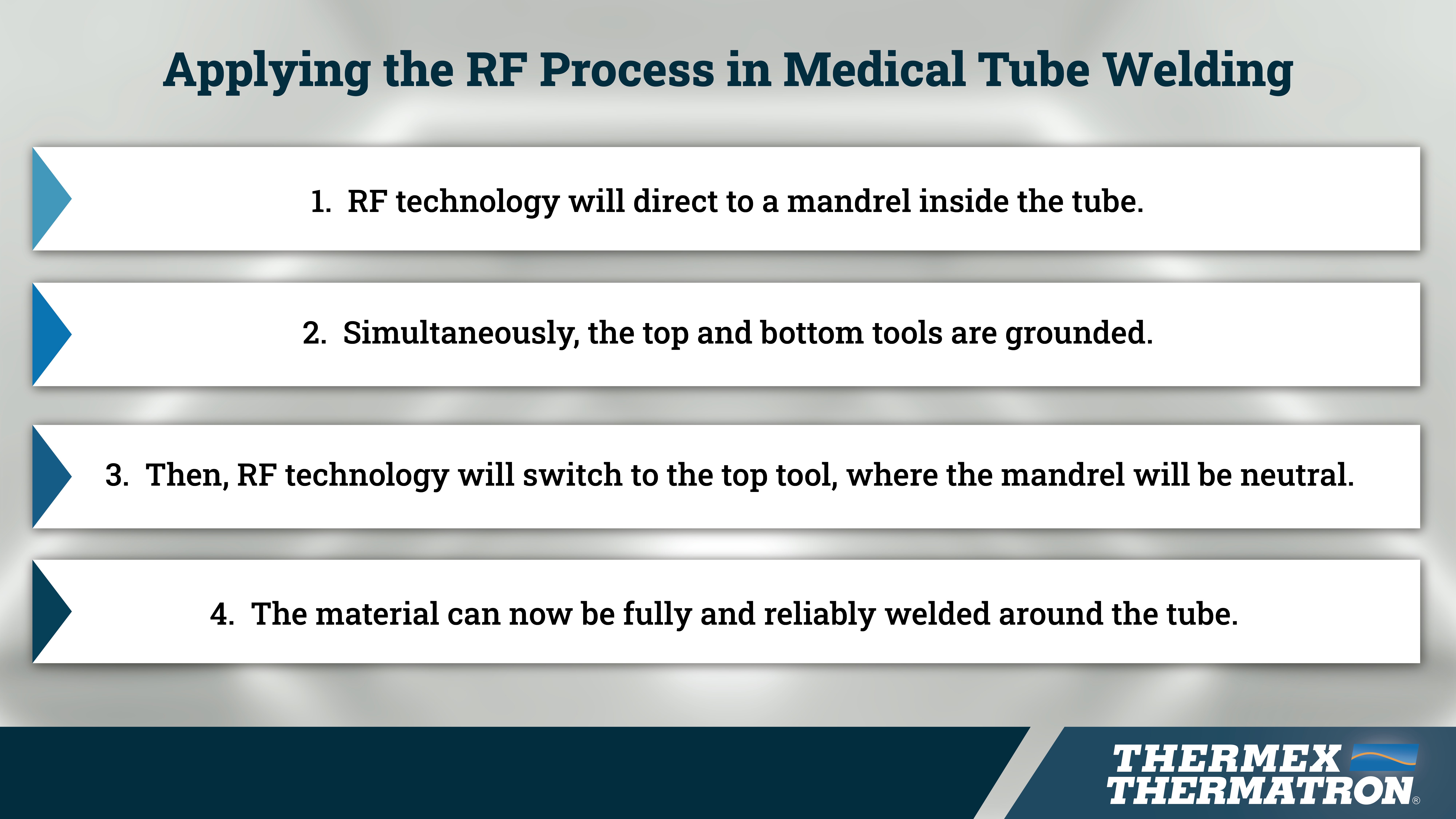
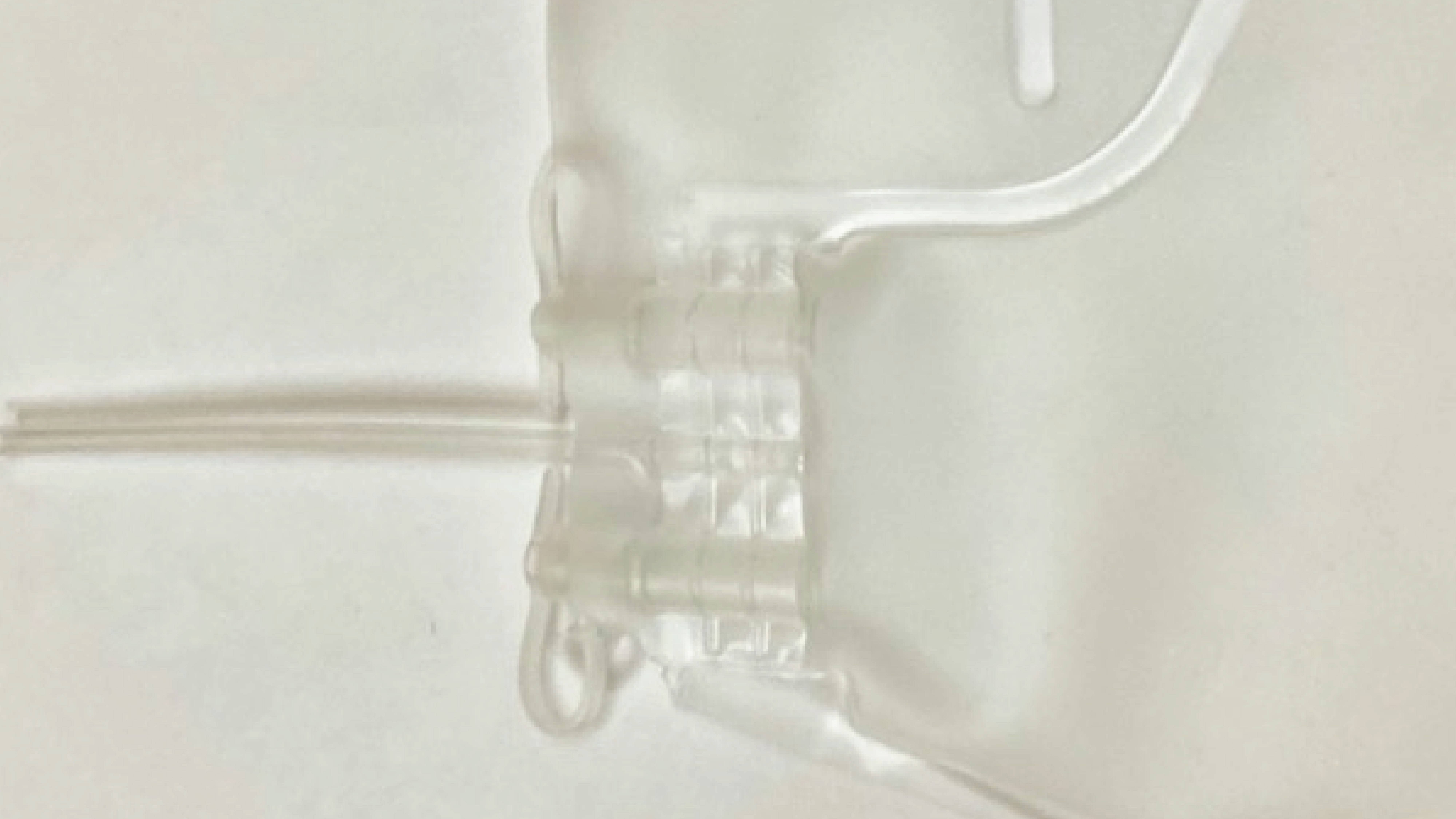
Sample of a Tube and Mandrel Heat-Sealed together with a Medical Bag
The Invaluable Thermex-Thermatron Advantage: Adopting a Manufacturing Alliance
Pioneering decades of experience and the powerful resources to design and build globally trusted equipment, Thermex-Thermatron designs and builds transformative technology; tools that run effectively for manufacturers, no matter the need, consistently producing low scrap rates. Purchasing an RF System is a key investment; one where manufacturers benefit in turning to a team of capable industry leaders.
As the backdrop of shifting pressures and variables escalate demands throughout growing industries, drawing on state-of-the-art technology can separate factories that achieve rapidly escalating demand from those scrambling to keep up; where the ability to precisely and rigorously deliver on quick results will be safer for assembly lines and end users alike. Understanding the depths of RF technology facilitates the production of reputable tooling — assisting manufacturers around the world in completing solutions set to fulfill ever-changing industry demands; with the support of a true manufacturing partnership.
For Thermex and Thermatron inquiries, contact our Director of Sales, Dean Mancuso (Sales@thermex-thermatron.com; 502/916-8972 or 502/243-5636).
For FIAB and Oteman inquiries, contact our Director of Business Development, Traci Evling (Traci@thermex-thermatron.com; 502/916-8981 or 904/662-2169).