TOP 5 RULES TO OPTIMIZE RF HEAT SEALING DIES
Thermex-Thermatron Systems
Thermex-Thermatron has over 80 years of industrial experience as a leader and innovator in the radio frequency (RF) and microwave (MW) technology arena. On the production floor, a combination of the right equipment and the right practices will yield efficiency, accuracy, and safety. Here are 10 crucial pointers condensing a wealth of insights, teaching you how you can obtain superior results when using RF heat sealing dies.
RULE #1: LOOK INTO CAPACITY BEFORE YOU ORDER YOUR NEXT RF HEAT SEALING DIES
Check the RF Heat Sealing chart to determine the capacity of your RF Equipment. This will help you determine whether the size of your run justifies the cost of multiple unit RF heat sealing dies.
RULE #2: WHEN YOU NEED TO ORDER NEW RF HEAT SEALING DIES — SPECIFY THE DETAILS
There always comes a time when you must order new RF heat sealing dies. However, complications often lie in lack of attention to critical details. From awareness of equipment features to knowing what material and how much to spend to examine each step of the process accordingly, make sure to watch out for these six components.
- Specify the equipment brand, size and mounting hole centers, size of bed plate, and platen. Additionally, look into the need for a heated platen.
- Identify the thickness of plastic to be used and desired trim for tear seal waste (typically ¼” to be torn away after sealing).
- Specify any special effects.
- Send one or more of the following:
- Blueprints
- Patterns
- Sewn samples
- Send enough material for testing all phases of the project thoroughly.
- If used, specify which types of steel and height will be required for cutting dies.

RULE #3: WHEN PREHEATING DIES WITH PREHEATED PLATEN, START WITH 150º F
Before you begin utilizing RF heat sealing dies, prepare for optimum equipment performance by preheating that morning and adapting your temperature later. Keep in mind, for appliqué sealing, a heated platen is a must.
- For maximum efficiency of tools, at the start of each day, preheat the dies by setting the thermostat to 150 ºF.
- Maintain this temperature until your die heats up from use, and then cut back on the thermostat.
RULE #4: UNDERSTAND WHEN AND HOW TO BEST INSTALL STOPS IN DIES
There are two cases we recommend that you absolutely need to install mechanical stops in your heat sealing dies.
- When seeking a controlled penetration seal.
- In cases that necessitate appliqué sealing.
Regardless of what sealing process you choose, note that all mechanical stops should be fully adjustable.
RULE #5: CHECK THE SET-UP OF YOUR EQUIPMENT BEFORE AND AFTER USE
As celebrated photographer Sam Abell said, “It matters little how much equipment we use; it matters much that we be masters of all we do use.” Any time you’re utilizing dielectric welding equipment, thoughtful regard to how you have set up your process will be a huge determinant of seals that get overheated, whether or not your seals are strong, and your die lines even. Pay careful attention to how you mount your dies, if your dies and trays are in the right operating sequence, and when to lower production’s time or power.
- Before mounting the dies, be sure to check that the head of your machine is level.
- To check equipment platen levelness:
- Place one (1) sheet of plain paper on the bed of the platen.
- Cover it with one (1) layer of carbon paper (carbon side against plain paper).
- Do not overlap.
- With the RF switch off, bring the upper platen with the die attached down on the carbon paper.
- Release and check carbon print on the plain paper for even die lines.
- Check to see that the dies and trays are set up in proper sequence of operation.
- To start test sealing:
- Start with low RF and seal time.
- Increase seal time first.
- Then raise RF and adjust air pressure. Do so until you have achieved your desired sealing strength.
- After production has been running for a time and dies are thoroughly heated to operating temperature, cut back on time or power gradually.
- This will prevent your seals from overheating.
For Thermex and Thermatron inquiries, contact our Director of Sales, Dean Mancuso (Sales@thermex-thermatron.com; 502/916-8972 or 502/243-5636).
For FIAB and Oteman inquiries, contact our Director of Business Development, Traci Evling (Traci@thermex-thermatron.com; 502/916-8981 or 904/662-2169).
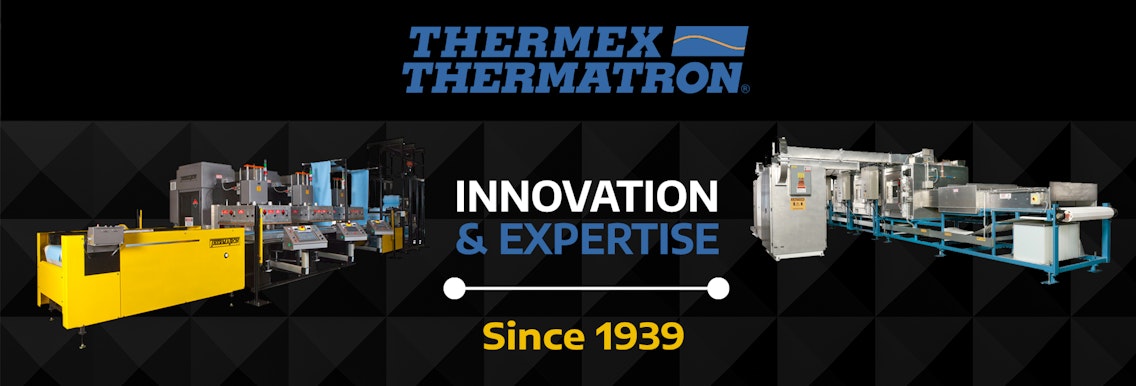