Thermex-Thermatron’s Practical Insights: How to Best Apply RF Pultrusion in Preheating
Thermex-Thermatron Systems
For over 80 years, Thermex-Thermatron Systems (“Thermex”) has commercialized leading applications that have helped advance dielectric heating processes across industries worldwide. Thermex intelligently designs high-powered industrial radio frequency (RF), industrial microwave (MW), and industrial press systems — innovative, resourceful machines made to facilitate quicker production, enhanced quality, and significantly fewer costs.
When leveraging RF pultrusion in preheating, utilizing Thermex-Thermatron RF Pultrusion Preheaters allows you to optimize productivity, strengthening key composite materials on the production floor. Assisting your manufacturing team to fully draw on RF power during the pultrusion process, both safely and effectively, Thermex-Thermatron has assembled prime insights — empowering you to gain the most use of your RF pultrusion preheating machines.
Understanding the Power of Using RF Pultrusion: Uplevel Your Production Methods
Thermex’s RF Pultrusion Preheaters allow manufacturers to harness cost-efficient methods that quickly boost production of composite materials. The process of pultrusion is ideal for processing raw polymer materials, where a mechanical force pulls them into a profile die. The following are four valuable assets when you use continuous RF power during pultrusion, applying high-frequency heat uniformly to your materials:
4 Major Advantages of Applying RF Preheating in Pultrusion
- Speed: In most cases, line speed can be doubled or even tripled.
- Better part performance: RF preheating eliminates cracking that results from differential curing (core to surface).
- Greater product capabilities: RF preheating allows larger products to be produced; something that far surpasses production by any other means.
- Extending the life of your die scales back wear and tear of mold: The lower viscosity of preheated resin reduces the pulling force required, thereby decreasing wear on dies.
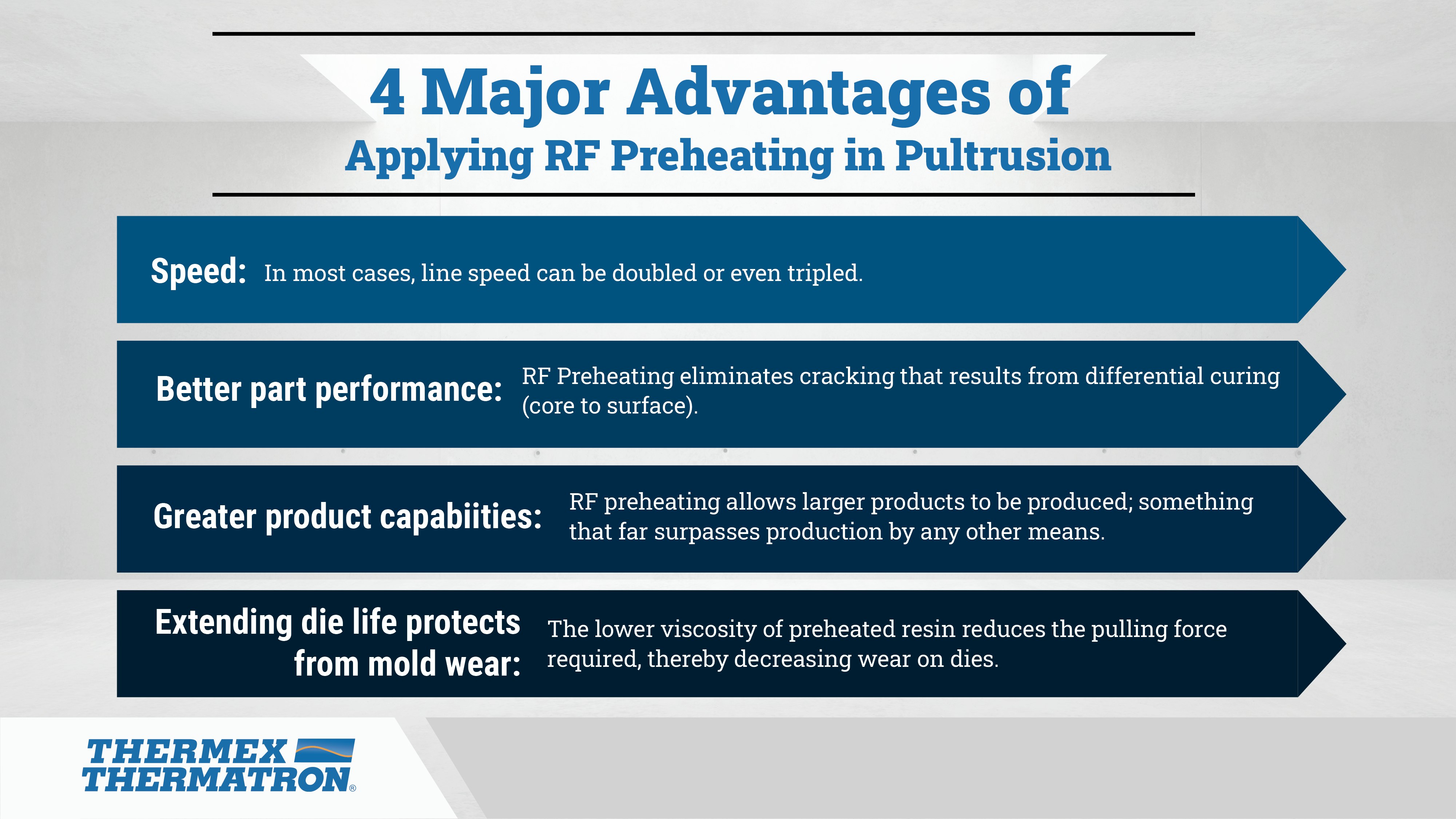
Utilizing Cutting-Edge Engineering to Achieve Sharp Precision
With a global reputation for built-to-last durability and transformative engineering made accessible, Thermex-Thermatron’s RF Preheater Systems set a novel standard for attaining accuracy and top performance in RF heating. When you operate robust equipment, capable of delivering heat that is not only uniform and swift, but offers you impeccable control, you elevate your ability to preheat pultrusion resin and reinforcements. Each of our systems is built to be as economical as possible when implementing in your production lines — all made here in the U.S.A.
Considered one of the quickest growing approaches to producing composite materials, Thermex’s multi-electrode model delivers a spectrum of choices, tailored for businesses to have production options. Offering a powerful 80 MHz in high frequency coupled with electrode height you can adjust, this intelligently designed machine’s spatial footprint is just marginally broader than our single-electrode model. When preheating thermosetting plastics for pultrusion, you can apply our multi-electrode model to create everything from composite structural components to large diameter fiberglass rods, sucker rods for petroleum, tool handles, and electrical insulators for power distribution.
When preheating, the possibility to access continuous RF power provides that much more focused heat when working with your materials (that are well-suited for RF heating). Additionally, the feature of an SCR Controller facilitates consistent, fine adjustment of power in addition to four electrode applicator controls — allowing you to apply any power necessary in uniform fashion to all loads needed.
With shop air pulled through an air filter (made to be replaceable for seamless maintenance), the machine cools itself. Built with a plate and grid current as well as DC Kilovolt meters, there are also options that include leading-edge IR sensors, a digital media display, and an over-temperature alarm for the utmost safety. When operating Thermex-Thermatron’s multi-electrode model, manufacturers are able to harness three phase high voltage, maximizing Solid State rectifiers enhanced with MOV compensation in a full wave; all in addition to bridge configuration.
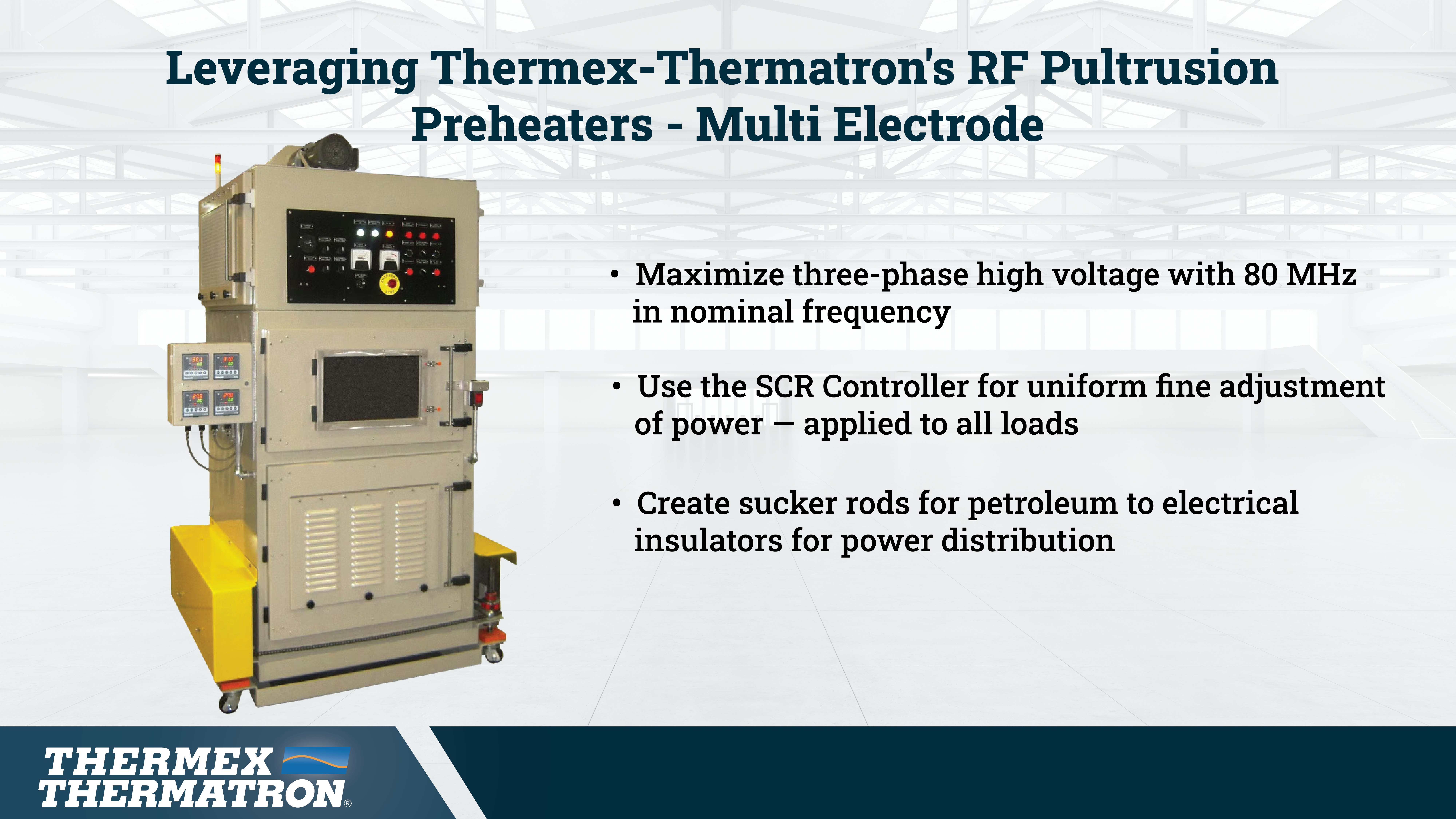
Eliminate Stress-Cracking When Manufacturing Reliable Products
Because Thermex-Thermatron Pultrusion Preheaters apply one of the top techniques to produce composite materials, it facilitates manufacturers who are conscious of saving costs to do so comprehensively.
When parts feature a thicker cross section, investing in quality dielectric heating equipment enables a company using a Thermex RF Pultrusion Preheater to focus heat on the inside of a part — before it ever enters the heated die. In doing so, this raises the line speed, simultaneously empowering manufacturers to enhance the quality of their products; lessening or counteracting the risk of a part stress-cracking. With voltage, output, and input power comparable to that of our multi-electrode model, our single-electrode model delivers this triple advantage with nominal frequency of 75 MHz and a slighter spatial footprint; complete with a laser, PLC, and remote start/stop function.
Manufacturers likewise can utilize the IR temperature sensor and display, built into the highly-engineered system’s control panel. Moreover, Thermex engineers designed the machine to offer automatic overload protection along with a tunable resonant cavity applicator, providing the ability to control how much power you seek to apply to every load. The Arc Detection System yields an audible alarm, protecting your dielectric materials from breaking down while also alerting you to safeguard equipment and processes. Whatever your product sizes are, working with a pultrusion preheater with adjustable spacing capabilities allows you to accommodate a variety of proportions.
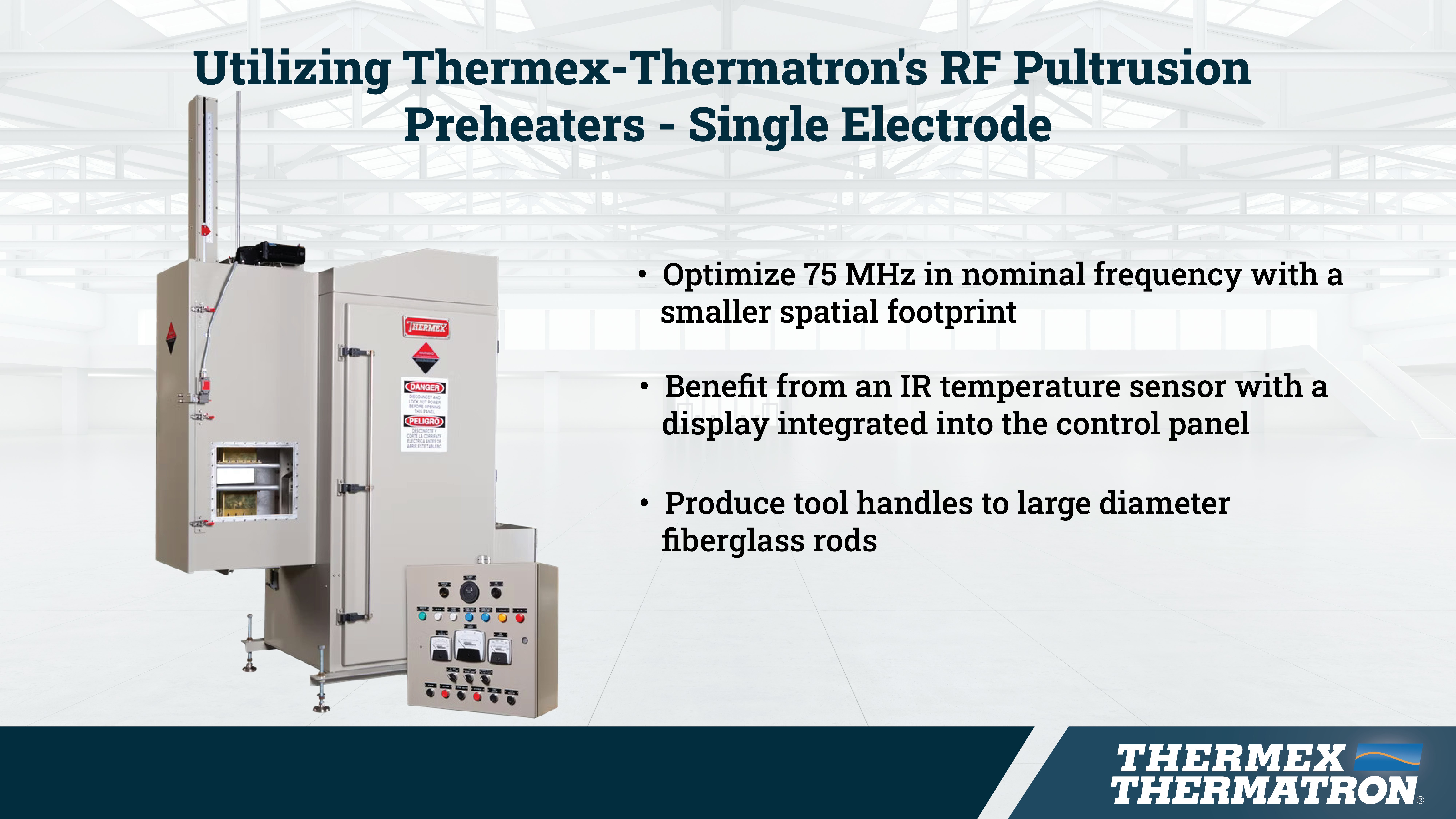
Gaining a Mastery of the Pultrusion Process
According to Expert Market Research, just last year, the pultrusion market circled $2 billion across the globe. Within the next five years, the market is anticipated to reach a value of about $2.7 billion. Globally sustainable, manufacturers are turning to this process more and more, converting liquid resins as well as reinforced fibers and assorted raw materials until they become fiber-reinforced plastic composites/polymers (FRPs); established through a pulling method through a heated die (unlike extrusion, which relies upon a pushing approach).
This manufacturing process helps factories seeking high-volume, expeditious production — continuous and viable. When utilizing a pultrusion preheater heightened with RF technology, not only can factories create long-lasting products, but they are also able to repeat uniform, durable results from product to product with rigorous agility. Because power is needed to pull materials through the die, accuracy is pivotal in determining the sturdiness and caliber of your finished profile. Utilizing a Thermex-Thermatron Pultrusion Preheater navigates that crucial precision for you with consistent prowess.
Applying constant pressure as the pulling process takes place, the objective is to melt the resins, impregnating them into the fiber reinforcements. From a resin bath to a heated pool, cross-linking commences, where the impregnated reinforcements become solid. Because the resin temperature surpasses the heat of the die, securing the ideal temperature is fundamental — for otherwise, this is the step where cracks can poke through the composite. When the temperature fails to rise to the amount necessary, cross-linking will struggle to fully take place, impacting the quality of your composite profiles.
Towards the conclusion of heating, separation initiates. To complete total separation, pulling machinery separates the die from the cured composite profile. Performing each step of the pultrusion process with value-added craftsmanship, innovative machinery built for efficiency and meticulous accuracy can transform the way you execute professional results on the production floor.
Supporting manufacturers in creating stronger, higher-quality products at a fast-tracked pace, Thermex-Thermatron has drawn on the dedicated expertise of over 80 years working with premier RF heating technology. Thermex-Thermatron’s dielectric heating equipment helps you heat thermoset plastics for pultrusion with advanced performance capabilities. To achieve uniform, streamlined production of your composite materials, applying RF preheating in pultrusion empowers you to streamline manufacturing processes — so you can navigate delivering output with finely tuned proficiency.
For more information, please visit our new website - thermex-thermatron.com.
For Thermex and Thermatron inquiries, contact our Director of Sales, Dean Mancuso (Sales@thermex-thermatron.com; 502/916-8972 or 502/243-5636.
For FIAB and Oteman inquiries, contact our Director of Business Development, Traci Evling (traci@thermex-thermatron.com; 502/916-8981 or 904/662-2169).