The Complete Radio Frequency Guide
Thermex-Thermatron Systems
Throughout the course of more than 80 years, Thermex-Thermatron has helped manufacture some of the most advanced industrial radio frequency (RF) and microwave (MW) systems for dielectric heating across the world. Compliant industrial RF to MW heating equipment manufacturing and use serve vital applications in aerospace, defense, and beyond. To help your team improve safety and efficiency, our seasoned experts made a complete radio frequency guide: assisting you in evaluating new and used equipment against dangerous emissions, sealing, as well as laminating and bonding.
Adopting Crucial Exposure Standards
In today’s increasingly safety-conscious work environment, it is not only important, but lifesaving to maintain radio frequency (RF) emissions at their lowest values — consistent with practical considerations for manufacturing.
At the very least, anyone using RF and MW industrial heating equipment should consider adopting federal and state OSHA guidelines, along with any internal RF emission standards, on the production floor. Every state’s OSHA regulations for compliance standards vary, so be sure to check your state's regulations.
For those who own and operate industrial RF welders, heat sealers, and preheaters as well as industrial MW ovens and dryers, the relevant federal OSHA regulation currently stands as:
(Standards - 29 CFR) Non-Ionizing Radiation. - 1910.97
Assuring That Used RF and MW Industrial Heating Equipment Is Well-Shielded
Recent and reputable manufacturing offers modern security for your industrial radio frequency and microwave heating equipment, created with current standards in mind. However, older or previously owned equipment is far less likely to have the shielding needed to comply with current standards.
When measuring compliance, remember that looks can be deceiving. Used equipment or equipment that has had its shielding removed or modified may appear to adequately function. However, this equipment can expose operators to RF energy scaling exponential levels above current standards. If touched while industrial heating equipment is in operation, the RF levels on control panels and surrounding metal structures can reach high enough to burn personnel.
Moreover, inadequately shielded industrial RF or MW equipment frequency interferes with nearby electronics. This type of poorly shielded machinery poses a risk of damage to exposed electronics, particularly if they are poorly designed.
Frequently, equipment 40 years or older will be retro-fitted with shielding to help increase its salability. It should also be noted that purchasing older equipment to then retro-fit it with effective shielding tends to cost almost as much as replacing it with new equipment entirely. When purchasing used equipment, buyers rarely have the expertise or the devices necessary to test and evaluate the equipment prior to purchasing. It's beneficial to consult an expert with the ability to assess the strength and weaknesses of your shielding — so you can trust that your investment will be worthwhile.
The Advantages of Upgrading to New RF or MW Industrial Heating Equipment
1. Low Radiation Emissions
New equipment emits a fraction of the RF energy compared to how similar equipment performed just a decade ago. Even so, the best designed and carefully built equipment still requires key maintenance. Industrial RF and MW equipment are no exception. When handling electronic and mechanical devices, proper care is not only required, but absolutely beneficial to maximize the equipment’s strengths.
2. Compliant, Powerful, and Peak Performance
Taking care that shielding maintenance stays up-to-date as well as keeping ground returns and neutralization in good condition are all essential. This is how to best prevent any degradation in performance — the kind of flaw that could result in noncompliance. These maintenance programs should be coordinated with the manufacturer.
3. More Effectively Maintained
Establishing a regular program for RF emissions testing will help you determine the effectiveness of routine maintenance as well as all shielding adjustments. Additionally, any users can purchase RF Survey/Industrial Compliance meters to check equipment for possible leakage. Another valuable option is to hire outside services for conducting regular surveys. Maintaining peak performance and minimum emissions is a careful balance. As such, only a qualified industrial RF or industrial MW equipment service technician should perform any repair services.
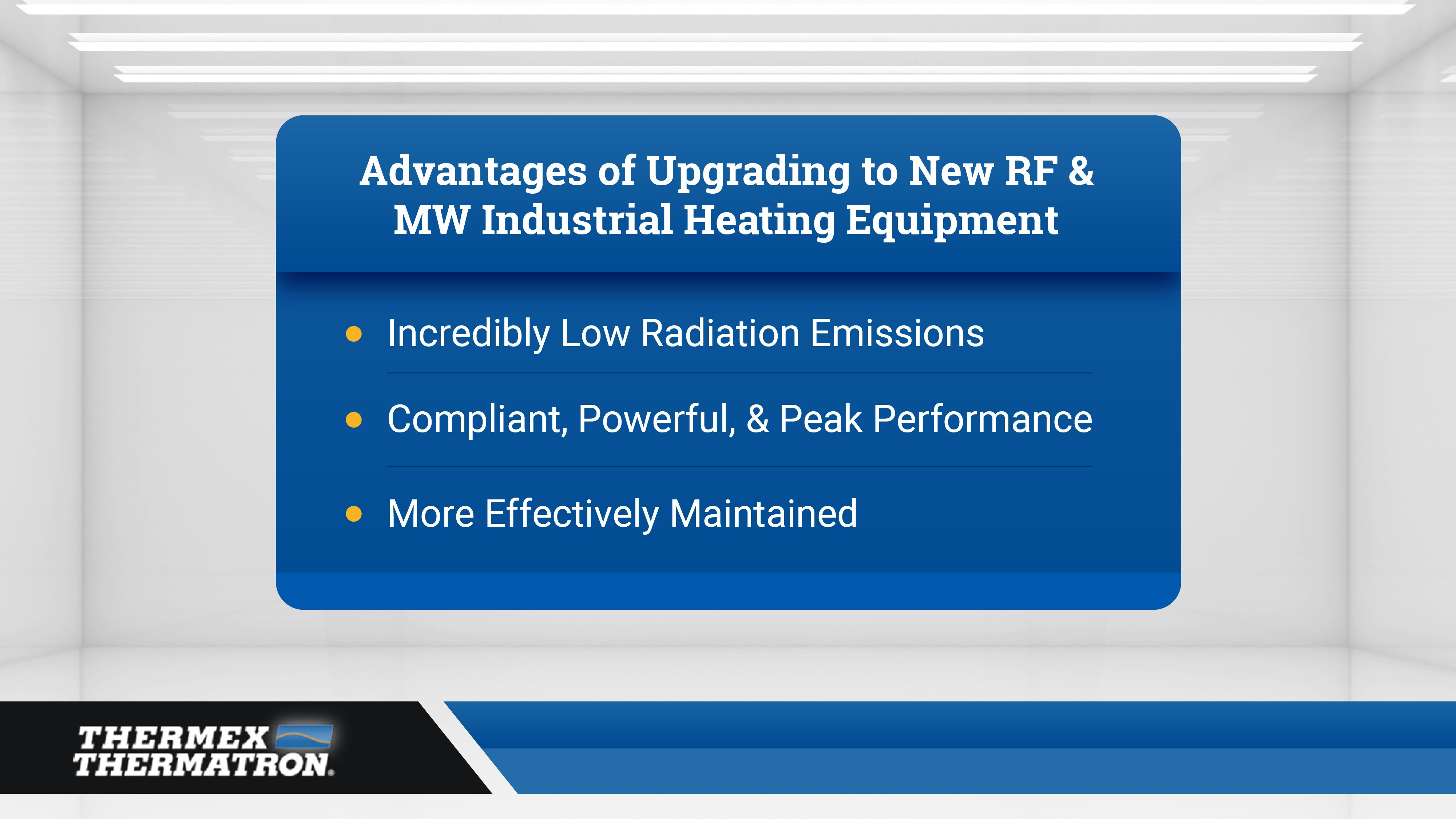
Optimizing RF Bonding and Laminating Processes
Combinations of aramid or glass fibers with a thermoset resin go on to create essential materials. As such, the importance of quality composite processes increases every day. These materials are critical to aerospace and defense technology, where human life is in the balance. In addition, bonding and laminating RF materials is utilized across the globe in body armor, ballistic composites, and in some cases as an asbestos substitute.
While the enhanced performance of composites fulfills central needs, it can also create singular challenges for manufacturers. The very properties desirable in the above applications, such as high thermal resistance, may be the qualities that complicate production. An asset like high thermal resistance can slow the manufacturing process in cases like structural honeycomb, ballistic, and laminated glass panels.
That said, in a wide variety of processes, radio frequency heating, when used with practical knowledge and experience, can lead to strategic advantages. Notably, in the RF heating process, the heat is developed directly in the materials being processed. Since the heat does not have to “soak in” from the outside, this significantly reduces thermal gradients as well as cycle times. When products require both heat and pressure, RF heating is not only suitable, but ideal.
Top 4 Values of Utilizing an RF Press
1. Shorter processing times. In most cases, production speed can be doubled or tripled.
2. Even curing — without overheated or uncured areas.
3. Reduction in internal stresses from differential curing; core to surface.
4. Larger products can be produced than the limits of using traditional thermal presses.

Relevant Tips and Calculations to Navigate Radio Frequency Sealing
For any given thickness of plastic, it is necessary to know the total electrode area in contact with the material. This helps you calculate the amount of RF power needed to fulfill the job. Keep in mind, thicker plastics will require less power than when you use thinner plastics.
The above figures are based on three decisive characteristics:
- Good quality vinyl
- Compact dies
- A seal time of approximately four seconds
To calculate the square inch area, measure the length of your bar in inches and multiply by width in inches. For example: A bar that is 36” in length by ½” in width has a total area of 18 square inches. We recommend using a heated platen or heated electrodes. When you do so, efficiency will increase by approximately 10%, proportionately also increasing the square inch area.
Profile of a Typical Seal and Tear Die (as Used for Loose-Leaf Binders)
To calculate the square inch area of your die, multiply the total length of the seal by the width as follows:
- Calculate the width of the seal portion as 1/32” times the length of your seal.
- Always calculate the tear seal as equal to 1/8” length of the seal. However, know that this will require more power due to the difference in height.
For example: If one page of printed paper were surrounded by a 1/32” seal and tear seal die, its square inch area would be 8 1/2“ x 2 = 17 and 11 x 2 = 22. 17 + 22 = 39 linear inches.
- Seal: 39 x 1/32” = 1.22 square inches
- Tear: 39 x 1/8” = 4.88 square inches
- 1.22 + 4.88 = 6.10 square inch die surface
We Can Produce Your Next Upgraded Industrial System
Following over eight decades as the premier developer, builder, and manufacturer of industrial systems, Thermex-Thermatron has developed the insights to create high-power RF welding systems for heating dielectric materials. We use our varied industry experience to deliver intelligently designed systems made for safe work conditions, well-shielded and adhering to current standards, and built to reduce processing times while elevating speed on the production floor.
Hands-on understanding in heating dielectric materials for radio frequency (RF), microwave (MW), and thermal applications allows us to commercialize new and needed applications. Thermex-Thermatron also shares this expertise around the world to bolster existing processes.
For Thermex and Thermatron inquiries, contact our Director of Sales, Dean Mancuso (Sales@thermex-thermatron.com; 502/916-8972 or 502/243-5636).
For FIAB and Oteman inquiries, contact our Director of Business Development, Traci Evling (Traci@thermex-thermatron.com; 502/916-8981 or 904/662-2169).
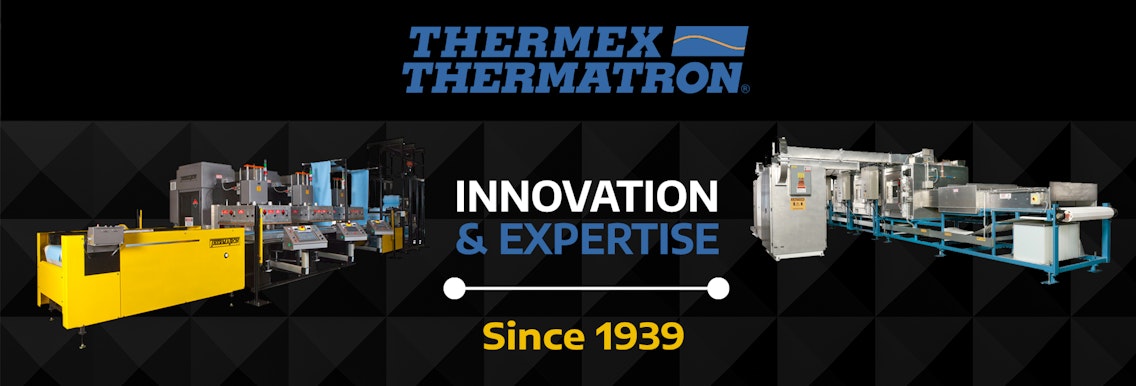