RF MAINTENANCE GUIDE
Thermex-Thermatron Systems
Even the most sophisticated manufacturing equipment has something in common with the ordinary lawnmower: If the operator wants it to work well and continue to do so, preventive maintenance must be part of the ownership of the equipment. No one who understands cars ignores the need for routine oil changes, and people know they should get medical check-ups before unseen conditions become urgent health crises.
While Thermex-Thermatron delivers world-class engineering and durability with every product it ships, our RF welders and sealers are no different: To ensure as much sustained, downtime-free operation as possible, certain preventive maintenance steps must be taken throughout the life of the equipment.
Moreover, failure to properly maintain equipment could result in the delivery of faulty or sub-par products to your customers, potentially damaging valuable business relationships at worst and requiring costly replacement orders to be fulfilled at best
At the same time, Thermex-Thermatron understands that during busy production times, routine maintenance easily can become anything but routine. Operators may be inclined to postpone small steps until a malfunction or breakdown occurs. When that happens, expensive repair costs can result and customer deadlines may be missed.
That’s why Thermex-Thermatron has produced a series of guides to help operators better understand and execute scheduled maintenance. The goal is to outline the various steps required and to outline them in a specific, easy-to-follow schedule that ensures every item can be completed with simplicity and confidence. Additional documents available on our new website - Thermex-Thermatron.com - address other products in the Thermex-Thermatron catalog.
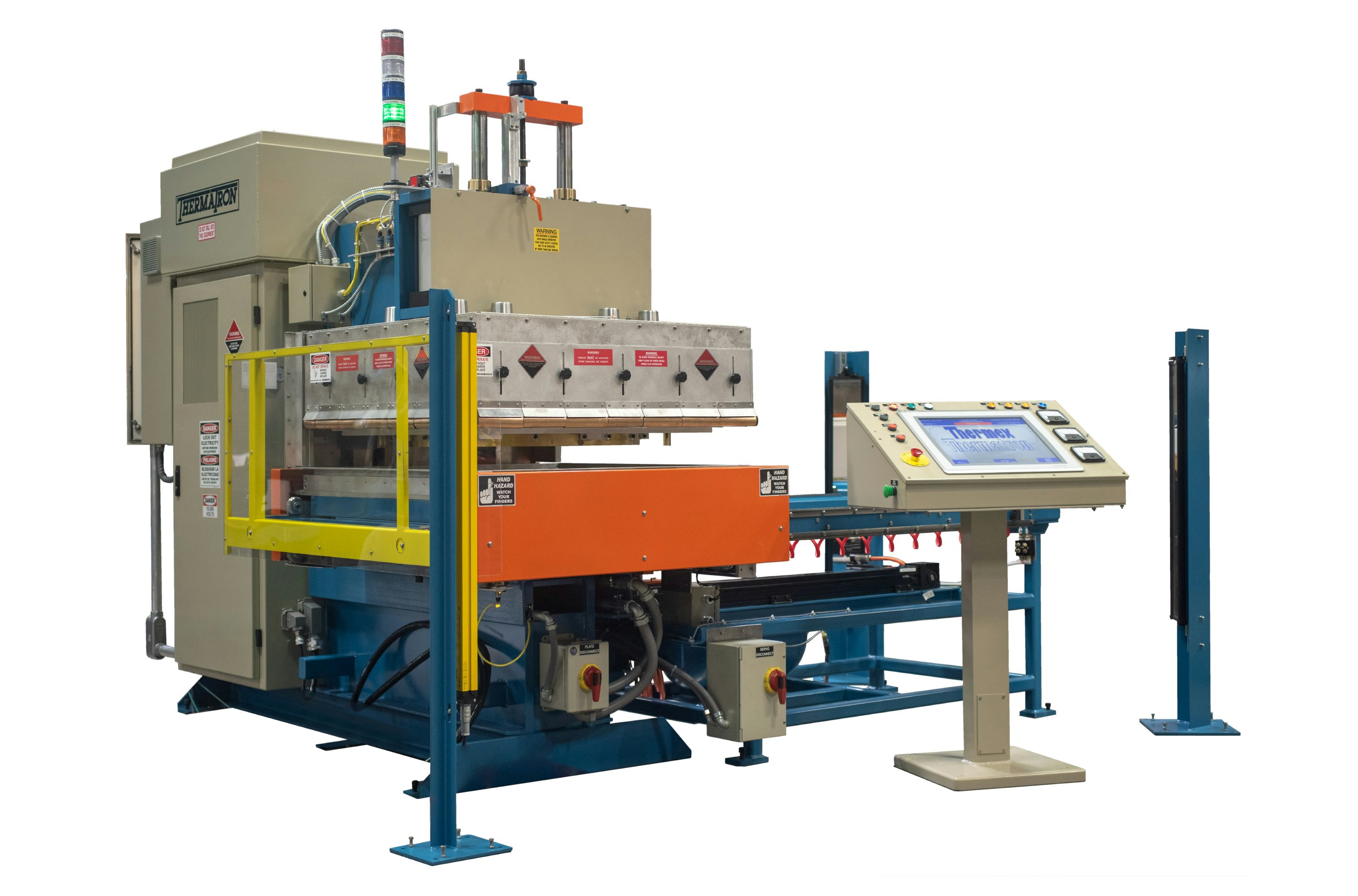
Notes:
Review and follow all safety procedures prior to performing any maintenance or service. Under NO circumstances shall personnel place any part of the body inside the RF generator cabinet until electrical power to those systems have been DISCONNECTED AND LOCKED OUT.
The list below shows an example of a maintenance program for the RF system. The list of items mentioned below should not be interpreted as inclusive. New items must be added to the list as deemed necessary by the daily operation of the RF system.
Daily Maintenance Checklist
Before turning the equipment at the beginning of each work shift, the operator should make a visual inspection of the equipment. At no time should the operator reach under the press or into the equipment enclosure nor insert any object into it. If any of the conditions listed below are found, the operator should report them to the supervisor or designated person. Before turning on the equipment at the beginning of each work shift, the operator should make a visual inspection of the equipment. At no time should the operator reach under the press or into the equipment enclosure nor insert any object into it. If any of the conditions listed below are found, the operator should report them to the supervisor or designated person. The operator should:
- Visually inspect for damaged, broken, cracked or burnt parts in the generator cabinet, press, shuttle and on the main control panel.
- Clean the die, nest and loading tray surface from any arcing, contamination or material residue.
- Check for loose or dangling components, wires or hoses.
- Check for any physical damage (dents) to the press coax, ground straps, and shielding.
- Check for accurate indexing of shuttle stations and mating of tool and nest, if applicable.
- Check the air pressure at the Filter-Regulator-Lubricator (FRL) for the correct pressure and ensure that there is sufficient oil in the lubricator. If a self-draining filter is provided, check for proper operation. If it is not operating properly, replace it. If a manual drain filter is provided or is used to replace the self-draining filter, check and drain, if necessary.
- Before turning on the electrical power, turn on the air pressure and listen around the cylinders for leaks.
- During operation, observe the press to insure that the platen raises and lowers evenly and smoothly.
Weekly Maintenance Checklist
Supervisors should designate at least one day a week for the following items.
- Clean the equipment once a week or more often if plant conditions require it. The single biggest factor in maintaining continuous operation of the equipment is keeping it clean. Dirt and corrosion can cause relay contacts to become inoperative and lead to deteriorated insulation, poor cooling, etc. • Because many parts of the unit cannot be reached with a dust cloth, dry, clean compressed air is the best cleaning medium. Factory compressed air can be used only if it is free from moisture and oil. When using compressed air, care should be exercised to prevent dislocation of delicate parts. • A light vacuum cleaner can also be used to clean dust and other solid contaminants. Blow or vacuum dirt from the relays, tube, and condensers. Check and replace the air filter, if necessary. • Finally, all insulators, tubes, etc., should be wiped with a clean, dry cloth. Any dirt that remains on the surface of these parts should be removed with a nonflammable cleaning solvent. It is important to select a solvent that does not leave a film residue or react to the material that is cleaned.
- If the blower wheel becomes coated with grease or dirt, it should be cleaned. It otherwise will become unbalanced and cause vibration and bearing wear.
- Check for leaks in the pneumatic system at all permanent connections, valves, gauges, sensors, and quick connects. Repair immediately, if leaking.
- And lastly, clean all of the door contacts and check for correct contact between the doors and the door frames to insure that no RF energy escapes into the environment.
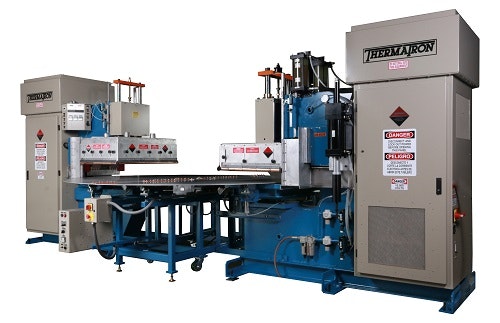
Monthly Maintenance Checklist
Finally, at the start of each month or when it’s otherwise convenient, it is important to perform additional minor maintenance checks that need to be done less frequently.
- Check and tighten any nuts or bolts that may have become loose.
- Check for good metal-to-metal contact between all high frequency components and between removable covers, shield contacts, and base plate.
- Relays and contactors should be checked for freedom of operation. Manually operate each relay (power off) to determine if it is mechanically free.
- Keep the applicator (press) in good operating condition. Check the press leveling and support bolts and tighten if become loose.
- The electrode should be thoroughly examined. The entire surface should be clean and smooth to reduce the possibility of arcing. The press guide should be lightly greased.
- Lastly, the insulator assembly between the hot electrode and upper platen should be thoroughly examined and cleaned. Carbon tracks are indicative of arcing and should be thoroughly removed. The probability of future arcs is greatly increased after a carbon track has been formed or dirt has accumulated.
Conclusion
It can seem like it is never a good time to stop production or delay the start of a shift to perform the routine maintenance checks as described above. True, there is the investment of a small amount of productivity into completing the steps. However, that small investment will seem minor against the time required to perform larger repairs or the expense of replacing equipment.
Begin following these recommended maintenance checklists immediately. If you identify any issues during the inspection that can’t be solved using our recommended tips, call our Service Department at (502) 493-1299 x207 or email us at service@thermex-thermatron.com.
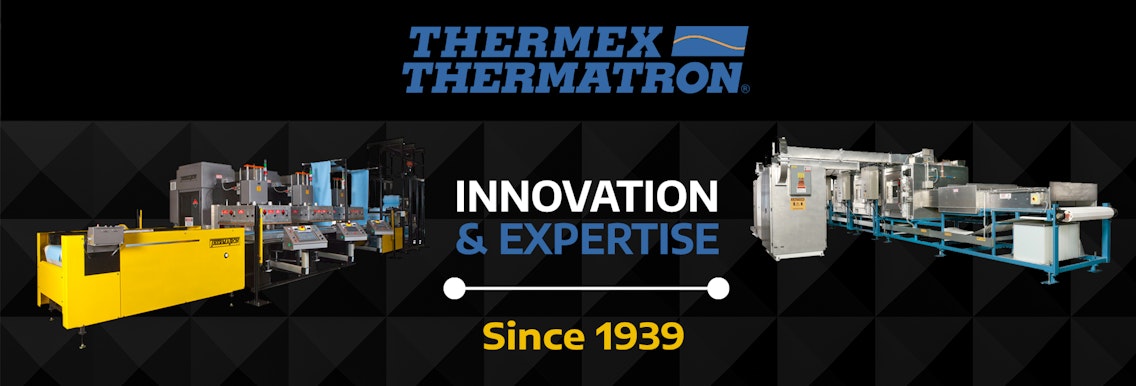