RF Buffer Materials
Thermex-Thermatron Systems
Top 5 Reasons Your RF Buffer Materials Aren’t Working
Whether designing, engineering, manufacturing, or servicing, Thermex-Thermatron has worked on many of the world’s leading, most advanced Radio Frequency (RF) and Microwave (MW) Systems. Understanding the properties of RF buffer materials is key to manufacturing well-made, lasting products. Following over 80 years of firsthand experience, here are five critical tips: discover the impacts of using the right RF buffer materials and how to catch common problems.
What Are RF Buffer Materials?
RF buffer materials are electrical and thermal insulating materials designed to cushion one or both sides of a die — acting as barriers to protect what you’re sealing. This can help you achieve the following benefits in production: less heat loss, stronger seal quality, and lower potential for arcing and burning. Most applications require some form of buffer.
Radio frequency buffer materials are available in sheets, rolls, as well as tape. If you are using tape, tape directly on the bed plate, electrode, or skin sheet. If you are using a sheet, you can place it on the bed plate of your press, where the sheet is usually held in place with masking tape.
How Do They Help?
Applying sheets and/or tape in your sealing process presents four main advantages:
- Lock in the heat and scale back on power: Doing so prevents heat loss due to a cold bed plate. When buffer material is used, this normally translates to lowering power consumption.
- Avoid damages from overheating: Buffer materials help to prevent arcing due to over sealing, uneven electrodes, or uneven plastic material — keeping the current in the location it’s intended.
- Focus the center of heat: This aids in concentration of heat with varied thickness of materials, or when sealing materials of different thickness. leading to more uniform product results.
- Make materials less sticky: Using sheets and/or tape is an effective way to eliminate any sticking of materials (silicone release paper or TEFLON), protecting your product from surface marring.
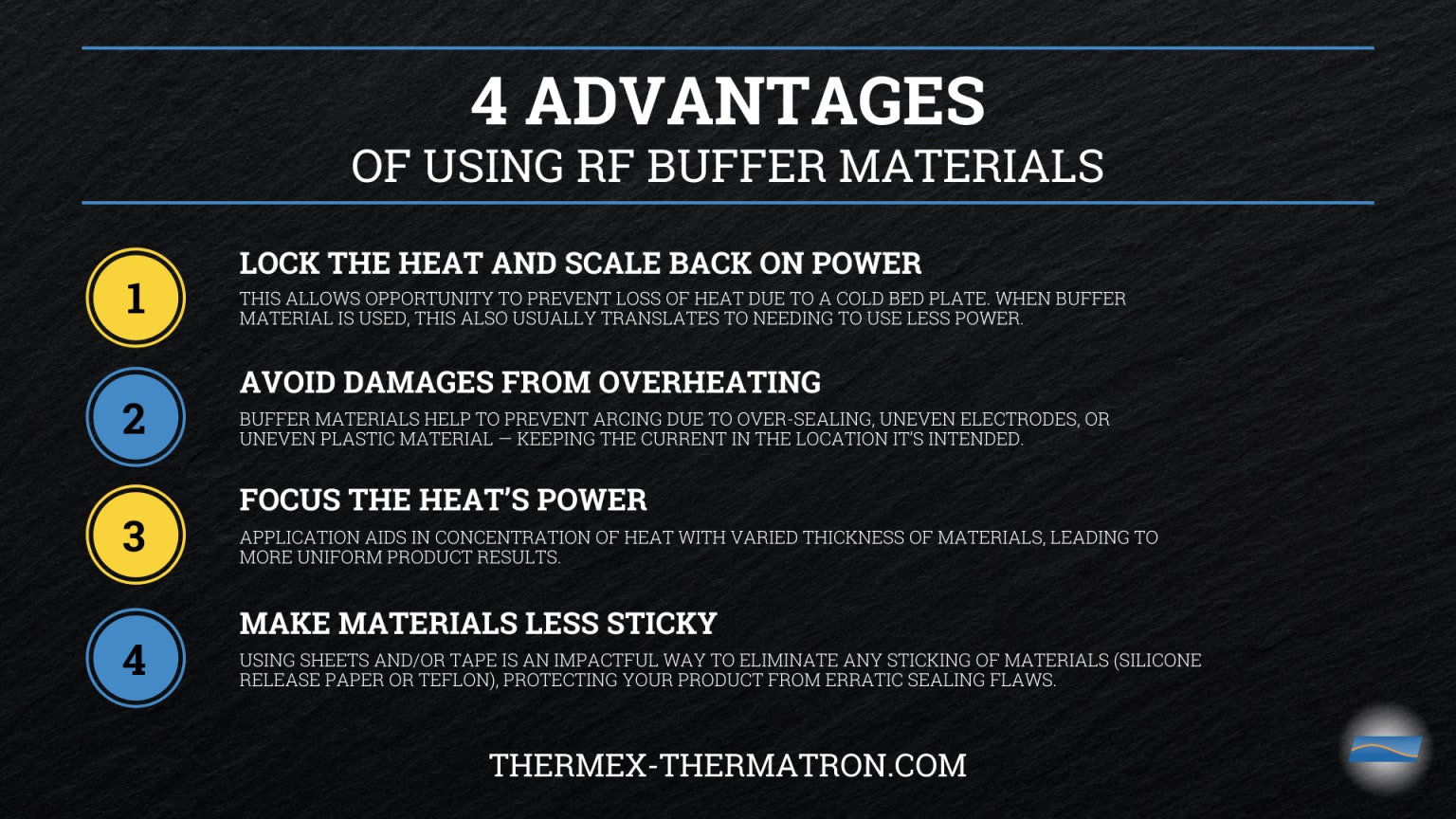
Types of Buffer Materials
Drawing from practical experience and knowing the type of surface desired on welds will help you select the kind of buffer you need. Here are different buffer materials that you can use on the production floor to make customers to take notice of your product’s outstanding quality and sturdiness:
- Phenolic (Bakelite)
- Mylar sheet and tape
- TEFLON sheet and tape
- Fish paper
- Glass cloth
- Silicone release paper
- Polypropylene 0.005
These materials may be doubled, if necessary.
The total should not exceed 0.030 inches.
Durability will be contingent upon the style of buffer you choose. After all, not all buffers are made alike. Some buffer materials will last several weeks, whereas others will wear out quickly due to cutting, or imprinting. It is important to always clean the die and bed plate after sealing: this helps protect the lasting quality of your buffer materials. If you find a hole has burned or cut through the buffer, that may be a reminder to clean or move the sheet. Sometimes, you can get extra use out of a buffer, turning over the sheet to use the other side.
What Causes Your Buffer Problems?
Issue #1: Irregularities
You encounter seals or dies that are uneven.
Probable Cause
Tape under the buffer is a likely culprit here.
Solution
Check below all surfaces. What you’re looking for is residue that does not belong. It is a valuable habit to clean completely after sealing; until you have removed all foreign matter.
Issue #2: Asymmetrical Cleaning Mishaps
Cleaning is an important protective measure, but sometimes it can result in seals that are uneven.
Probable Cause
Standing waves can lead to bumpy textures.
Solution
The best next step when you notice uneven seals is to check with a repairman or your factory personnel for resolution.
Issue #3: Cold Seals
You know you have encountered cold seals when the material has separated, not holding your product together the way you need.
Probable Cause
The material can separate if the buffer you used in sealing was too thin, or just the wrong type for what you needed. Additionally, if the power or pressure were inadequate, you won’t reach the temperatures required for strong seals.
Solution
Try other buffers and/or add double thickness to reduce your need for more power or pressure.
Issue #4: Opposing Materials Fail to Seal Properly
You have paired thin and thick materials together — and this incorrect combination is destined not to seal well.
Probable Cause
Without the right pairing of materials, this causes heat loss to your dies.
Solution
The best fix is to add a buffer to thin material, and this will help you shift the center of heat for better welding.
Issue #5: Arc Suppressor Not Operating Normally
Sometimes amid contact arc suppressor operation, you may find apparent bubbles are exposed. The biggest indicator you have a problem: your buffer is burning.
Probable Cause
Pinholes in your buffer cause sealing flaws like bubbles.
Solution
Take the buffer that has burned and replace with a new buffer. Check your arc suppressor for normal operation following replacement.

Providing Eight Decades of Experience Leading the Industry
Strengthen your RF heat sealing and welding processes with Thermex-Thermatron, which provides replacement buffer materials including Mylar, Teflon, silicone, Kapton, and fiberglass. Thermex-Thermatron builds high-power industrial microwave systems, radio frequency, and thermal heating systems. We engineer, manufacture, and assemble each product at our 40,000 square foot facility in Louisville, Kentucky.
Every perspective we suggest comes with the benefit of over 80 years of experience leading this industry and learning how to sharpen manufacturing quality and productivity. The best way to improve production is to understand its common challenges, and to meet those challenges with innovation. That’s why we have an in-house laboratory, ThermaLab, where we are equipped to test assorted materials on various radio frequency and microwave systems. We share these insights with our customers, equipping them with powerful solutions to enhance their radio frequency and microwave production processes.
For Thermex and Thermatron inquiries, contact our Director of Sales, Dean Mancuso (Sales@thermex-thermatron.com; 502/916-8972 or 502/243-5636).
For FIAB and Oteman inquiries, contact our Director of Business Development, Traci Evling (Traci@thermex-thermatron.com; 502/916-8981 or 904/662-2169).
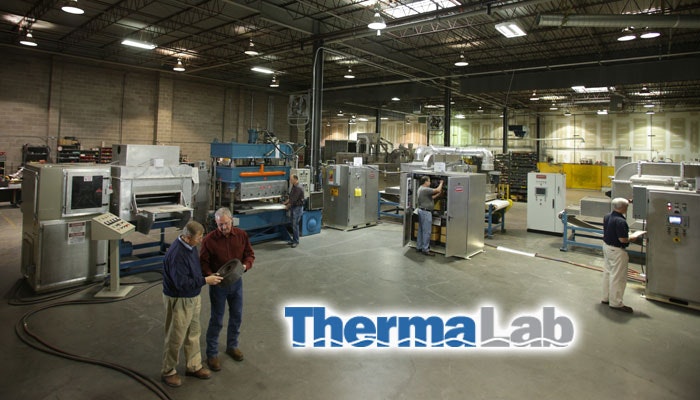