Optimizing RF Welder Performance
Thermex-Thermatron Systems
Radio Frequency (RF) welding and sealing systems are an efficient and reliable resource for strengthening industrial manufacturing processes. However, for those just getting started with this machinery, it can be intimidating. Dielectric heating properties and sophisticated electrical controls take time and practice to master. Studying the RF heating process will help operators optimize RF welder performance, work with confidence, and get the most out of his or her time and materials.
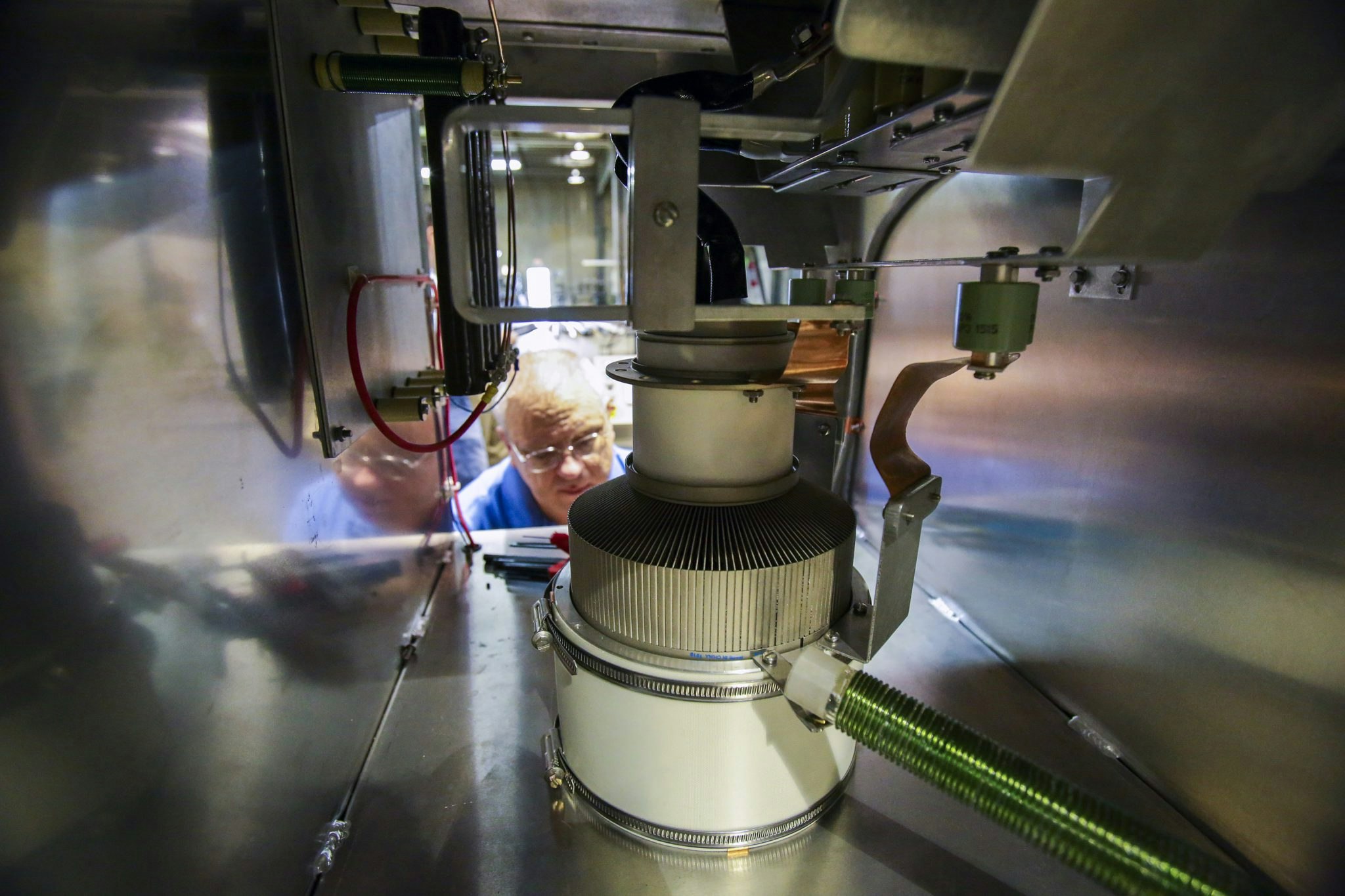
Understanding Dielectric Heating Properties
Dielectric heat sealing, otherwise known as high frequency or RF welding, uses electricity to generate heat within a material instead of forcing heat into it from the outside. The amount of heat generated internally is dependent upon the dielectric loss of the material. Materials with very low dielectric loss do not heat very much, even though the RF heat sealer may be turned on and fully functional.
The greatest effect can be observed where there is high dielectric loss in a material. This is most common in PVC and polyurethane materials, which can be heated and sealed almost instantaneously. Polyethylene and polystyrene, however, are examples of low dielectric loss materials that cannot be heated with RF welding equipment.
Understanding which materials will or will not heat well is an effective consideration when using RF systems. Heating selectivity through material choice can greatly optimize RF welder applications. When two or more layers of thermoplastic materials with sufficient dielectric loss are exposed to an RF field, they can be brought to a liquid or near-liquid state rapidly. These multiple layers can then be blended into a single layer, stronger than the individual layers themselves. Proper adjustment of the hardware, or controls, on your RF systems enables the user to manipulate the process variables and produce the desired result.
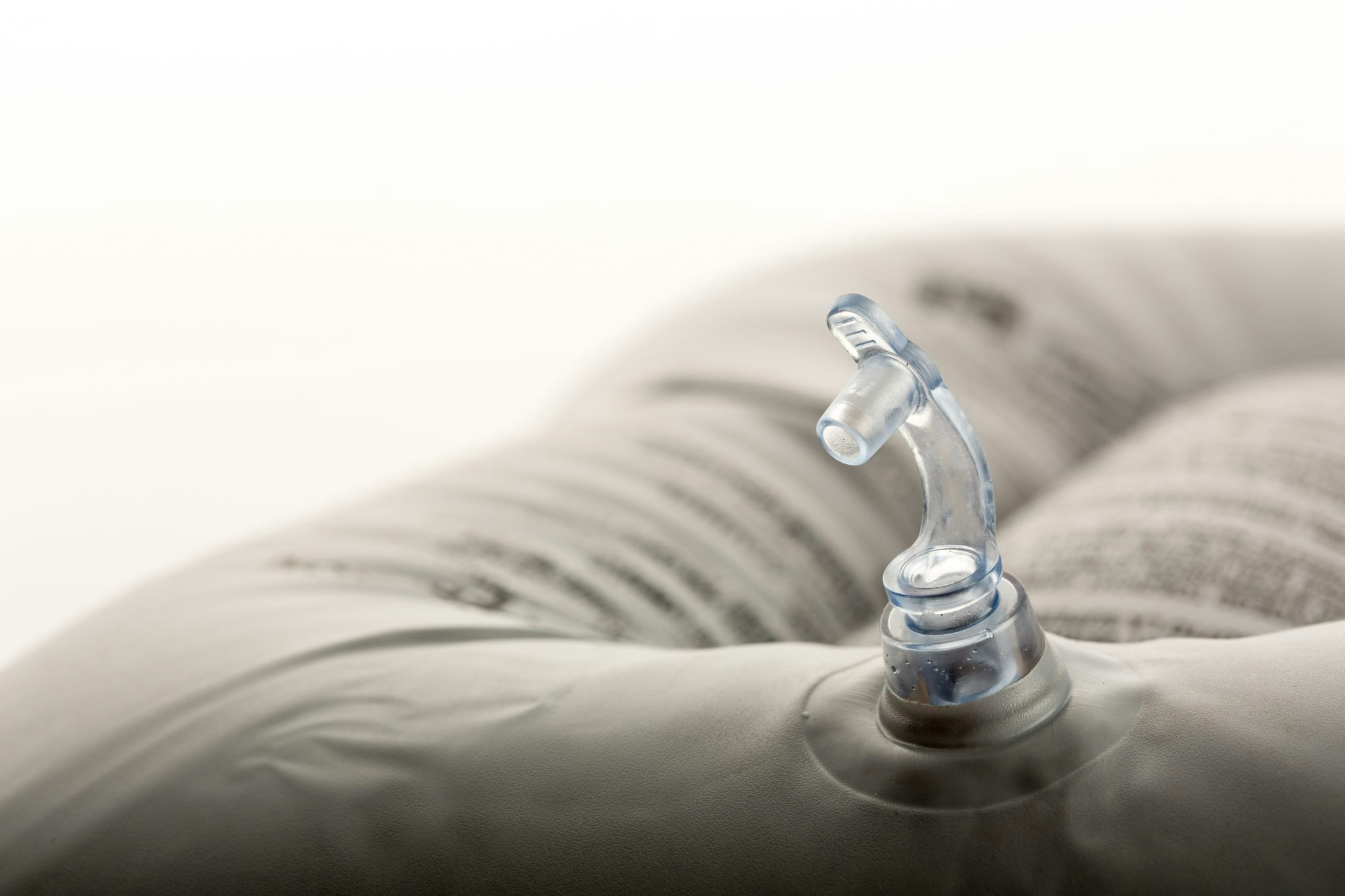
Parameters to Follow in Operating and RF System:
1- Pre-Seal Time is typically one to three seconds.
Pre-seal time is the amount of time that elapses after the press closes and before the RF heating cycle begins. The pre-seal time is used to allow the press enough pressure to stabilize and for the materials to come into firm and intimate contact. If the press is equipped with a heated platen, pre-seal time allows the tooling to transfer heat to the material. Heated tooling is used to relax stiff material for better contact, maintain constant tool temperature for first/last part consistency, or increase dielectric losses in materials for easier sealing.
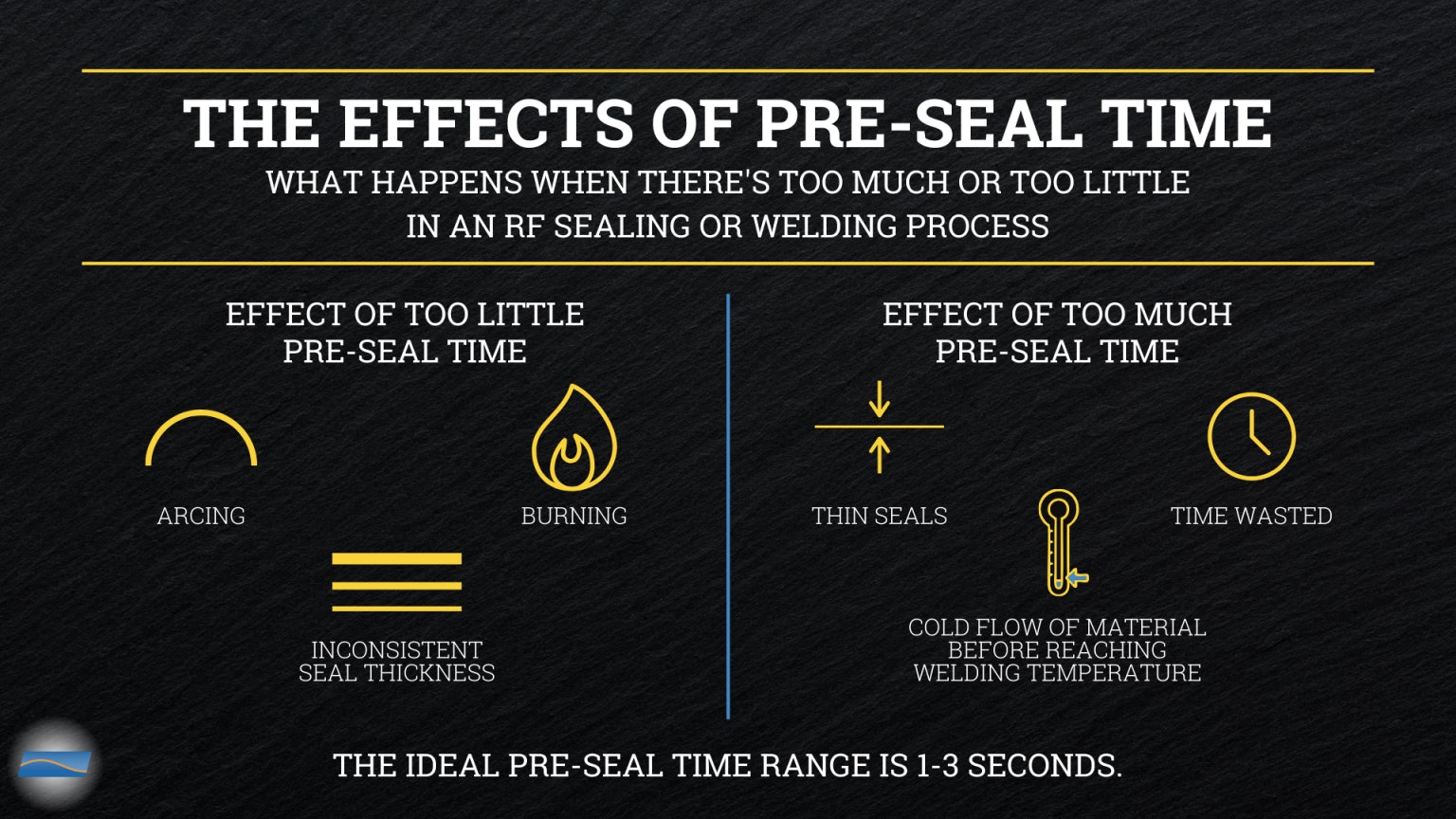
2- Seal Time is typically two to six seconds.
Seal time is the amount of time the RF energy is applied to the materials in order to perform the intended work of welding. Seal time interacts with RF power. Typically, RF power is adjusted to bring the seal time within a two to six second window.
If seal time is too little, there may be a poor weld or none at all, inconsistent weld thickness, delamination of materials, or a rough or no tear when using tear seal dies. If seal time is too much, the material may over-weld, arc, have a thin seal, excessive squeeze out, or bubbles.
3- Cool time is typically one to six seconds.
Cool time is the amount of time that the press remains closed after the RF power shuts off. This allows the molten material of the weld to solidify or quench before the press pressure is removed. The effect of too little cool time is that the product may stretch or distort when removed from the die, material may rebound, causing poor definition, which is particularly troublesome in embossing operations. The main disadvantage of too much cool time is simply time wasted.
4- Pressure is typically 30-80 Psig for average size tooling in a “C” frame press.
Pressure is required to bring the materials to be welded into intimate contact and to force the air from between the layers, and requirements vary widely based on application and materials involved. Once the material to be heated reaches a molten state, pressure moves the tooling to break the surface tension between the layers of molten material and mixes them, producing a weld.
When the pressure applied is too excessive, tooling can be forced through the materials before they are hot enough to break the surface tension between layers. This is referred to as a cold weld. The result of a cold weld is that the tooling reaches the proper dimension for a completed seal; however, the materials remain two discrete layers. Tension applied to the interface will result in delaminating and failure. Tear seal tooling is particularly sensitive to pressure adjustments in order to prevent cold welds, dulling of cutting edges, or cutting buffers. Superfluous pressure makes the finished part difficult or impossible to separate or tear out cleanly.
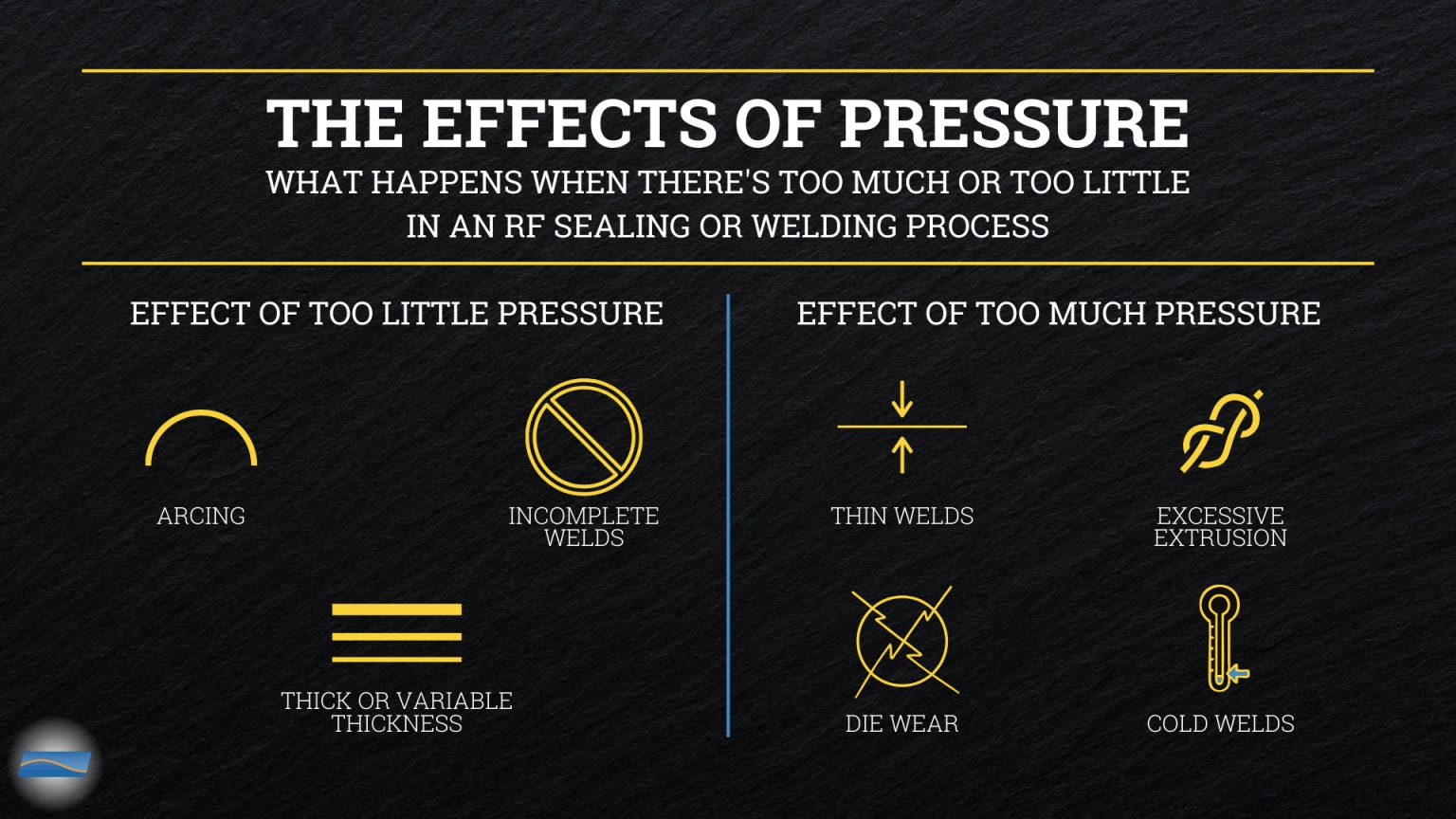
5- RF Power is dependent on the application, size, and materials to be welded.
The RF power level required for achieving optimum performance is that which melts the materials as quickly and evenly as possible with arcing, or dielectric breakdown. RF power requirements and RF equipment capabilities are ideally matched by the manufacturer in order to provide good value with adequate reserve for future applications.
Thermex-Thermatron offers RF Welders and Sealers with output power capabilities from 1.2kW to 40kW. These systems are ideal for industrial manufacturing with various plastics and fibers involved in the process. Our RF welding systems are intelligently designed to produce a strong and uniform seal on a wide range of materials, whether they are used for packaging, medical, fabric, or automotive products, and can be customized to suit a range of industrial processes.
For Thermex and Thermatron inquiries, contact our Director of Sales, Dean Mancuso (Sales@thermex-thermatron.com; 502/916-8972 or 502/243-5636).
For FIAB and Oteman inquiries, contact our Director of Business Development, Traci Evling (Traci@thermex-thermatron.com; 502/916-8981 or 904/662-2169).
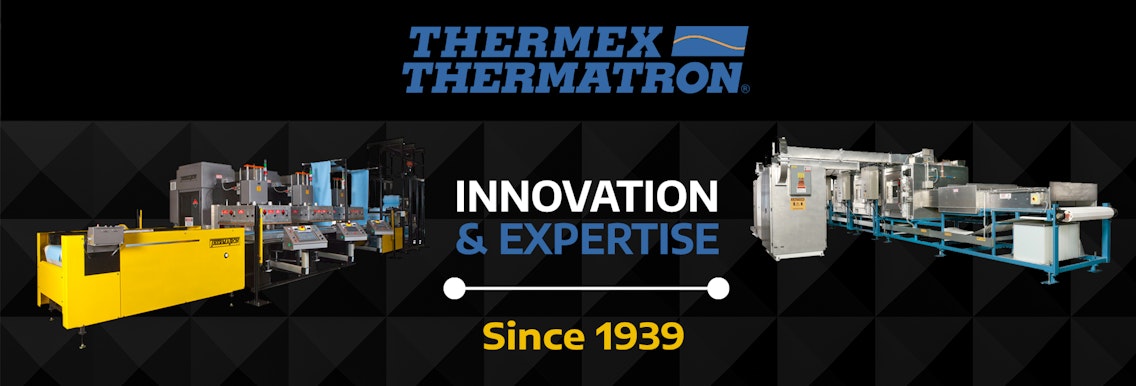