Answering The Call Of The Medical Industry
Thermex-Thermatron Systems
For over 80 years, Thermex-Thermatron has illuminated the path in exploring two massive fields: radio frequency (RF) and microwave (MW) technology. Knowing the background of RF welding — what it takes to secure precision welding — has helped steer the evolution of the medical products we use today. Here’s how an innovative, low-cost, and stellar-performing plastic called polyolefin is revolutionizing the medical industry for the better.
Finding Plastics That Suit Welding Needs: The Road to Reliable Medical Products
Consider that radio frequency welding relies on the vibration and orientation of charged molecules within the scope of a polymer chain — because without this happening, it’s impossible to generate heat. Product manufacturers need the right kind of plastic when using the RF process — the kind of plastic containing polar molecules that can resist the heat. For this reason, two of the most common thermoplastics to be RF welded are polyvinyl chloride (PVC) and polyurethanes.
The question becomes if what's commonly used is necessarily what's best when it comes to RF welding for life-changing medical supplies. Consider that each material carries differences in chemical properties; the properties that ideally suit one product could result in a total mismatch for another.
True, it could be feasible to use RF welding on different polymers, including nylon, polyethylene terephthalate (PET), ethylene-vinyl acetate (EVA), as well as some acrylonitrile butadiene styrene (ABS) resins. That said, the reason other thermoplastics become more frequently used is because the ones listed demand special conditions. Then come some polymers that are not at all suitable for welding: polytetrafluoroethylene (PTFE), polycarbonate, and polystyrene.
Even the popular thermoplastics like PVC pose impending restrictions that don’t make it easy on RF welders. That's why a special grade of polyolefin has been developed, carrying the powerful ability to be RF welded.
Good News for the Medical Industry
There are two major reasons polyolefins are being used extensively in the medical industry:
- Polyolefins are relatively low in cost — which can save production managers on expenses.
- Polyolefins contain unique performance properties.
○ Strong chemical resistance.
■ This protects the thermoplastic from corroding after enduring intense heat: empowering a polyolefin to maintain its original chemical properties.
○ Chemical inertness.
■ A special-grade polyolefin’s chemical properties won’t clash with other materials or take on toxic properties, which makes the end product safer to use.
○ Light in weight.
■ Because the material is lightweight, this makes polyolefins simple and cost-friendly to use, without sacrificing durability.
The top two most popular polyolefins are polyethylene (PE) and polypropylene (PP). These polyolefins are used in all kinds of applications: ranging from syringes to storage bags.
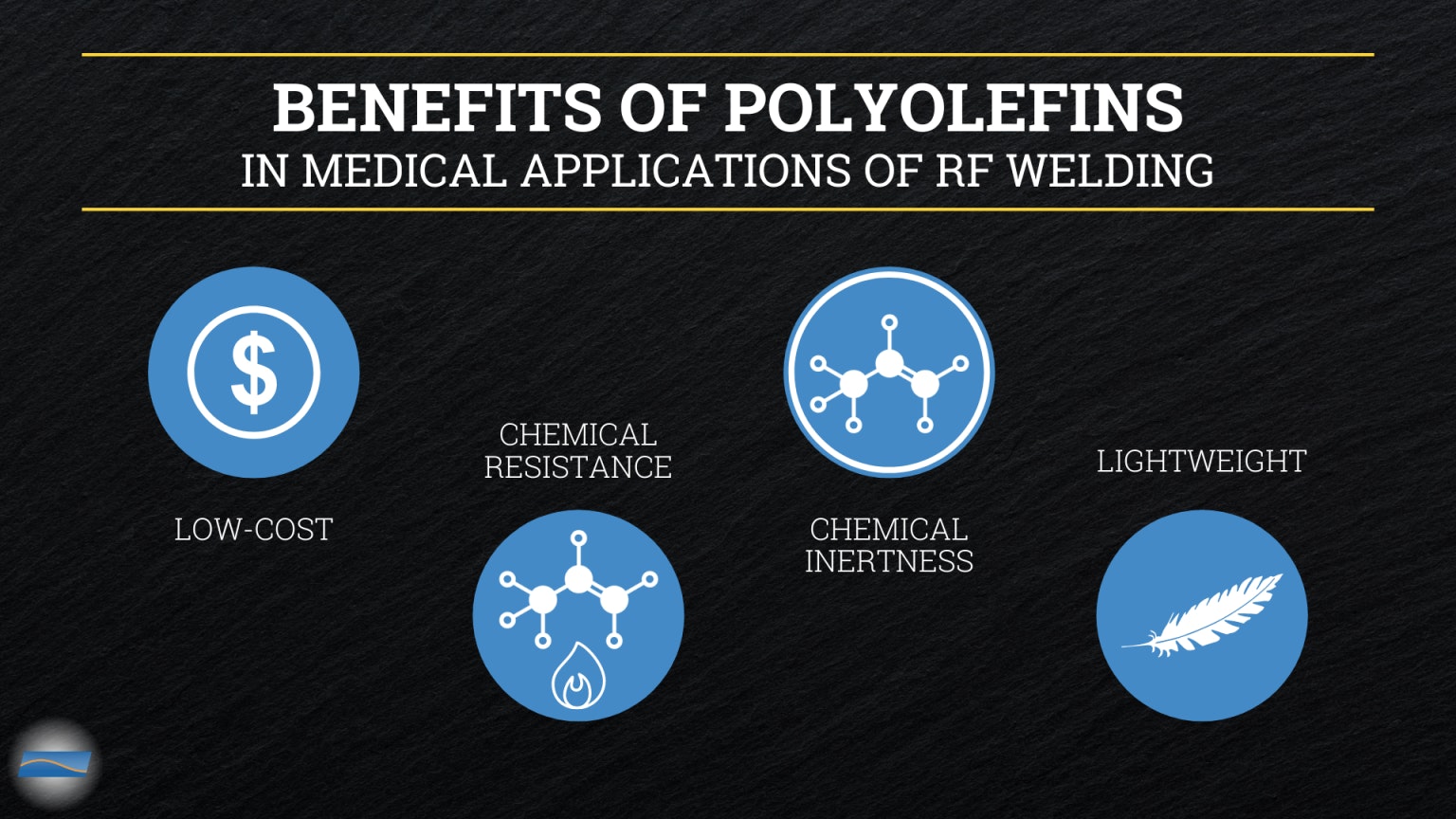
Melting Is Easy, But Bonding Isn’t: Combating Welding Challenges
While a noticeable ease of melting is a surefire benefit, it’s not all smooth. In fact, bonding polyolefin components can be challenging. This matters in the medical industry, where heat bonding is essential to the precision welding needed for products — and adhesives as well as solvents prove to be mostly ineffective. Yet, that’s exactly how the road to breakthroughs begins; and Thermex-Thermatron has seen more than a few improvements arise over eight decades in this exciting industry.
Learning to think outside the box of these welding difficulties, the medical industry turned to polyolefin films. For a number of years, applications like medical bags, protective sleeves, and wound care, among others, have leveraged polyolefin films. That’s where radio frequency lands brilliantly: these film-based medical constructions often utilize RF welding.
Recently, the demand for replacing polyvinyl chloride (PVC) films has been rising, because of concerns pointing to toxicity as well as plasticizer leaching. In the medical industry, this warning is particularly important to heed, as any toxicity could negatively impact a patient's health. Ever the innovators, industrial engineers responded with a new solution: creating multi-layer polyolefins along with new grades of polyolefins (specifically designed to enhance the exact precision welding the medical industry has been seeking).
Elevating the Positive Ramifications of the Welding Evolution
Welding for medical care products won’t stop evolving, and the advantages of change continue to spark new marvels for the medical industry. These efforts to improve welding and to meet the distinct needs of medical production have led to superior integrity in sealing — where RF welding stands at the core of many advances.
We take pride in Thermex-Thermatron RF Systems and RF Inline Systems as the right equipment to complement the best strengths of polyolefins. We’ve seen how different clients require singular products, which is why we custom-design all of our RF equipment to match every possible need.
We’ve created these systems so that they integrate RF technology and feel efficient for users, including beneficial options like a heavy-duty unwind stand, an automatic indexer, and multiple RF welder stations; supplying each with its own PLC with PC interface controls. Thermex-Thermatron produced this equipment with intention, so that every system feels perfect for welding from rolled materials for all kinds of medical products and devices: blood or IV cuffs to colostomy or enema bags.
Specifically, our RF Platen Press is a system that empowers medical manufacturers who need to complete thermoplastic sealing with efficiency and top-notch quality. Thermex-Thermatron’s RF Switching Network technology creates a unique possibility for a generator to maximize one press closure by achieving two full cycles — this includes customizing power levels to sealing times. The press incorporates our integrated switch, which facilitates the switching process at a preset power and time setting allowing control of the polarity for manufacturers sealing electrodes. Because the RF can be turned off here, this lowers electrical arcing as well as its hazards and flaws, resulting in a stellar outcome: an undeniably impeccable seal.
This translates to the medical industry, because a seal that’s balanced means bag outlines, tube insertions, as well as tear seals, can be realized with one press closure; ultimately, curbing the time and expense it takes to produce great products.
How Innovations Are Playing Out in a COVID-19 World
As a proud essential manufacturer at a time the medical industry battles the impact of COVID-19, we are contributing our crucial efforts: offering fundamental RF equipment to help brave medical manufacturers across the nation. More than ever, powerful, precise equipment is critical, as the industry calls for an influx of as many well-made, cost-effective supplies those leading the frontline can find.
There are ramifications seen all over the world, as medical manufacturing clients have expressed gratitude to Thermex-Thermatron Systems amid a challenging global climate. When there are innovations to the way we produce medical supplies, this means individuals overcoming COVID-19 diagnoses have the blood bags, IV bags, blood pressure cuffs, and more to come out on top.
Access to quality treatment can mark a profound difference for many lives, both here in the U.S. as well as across the globe. Thermex-Thermatron is committed to evolving with forward-looking RF technology: meeting the changing needs of this industry for many decades to come.
For Thermex and Thermatron inquiries, contact our Director of Sales, Dean Mancuso (Sales@thermex-thermatron.com; 502/916-8972 or 502/243-5636).
For FIAB and Oteman inquiries, contact our Director of Business Development, Traci Evling (Traci@thermex-thermatron.com; 502/916-8981 or 904/662-2169).
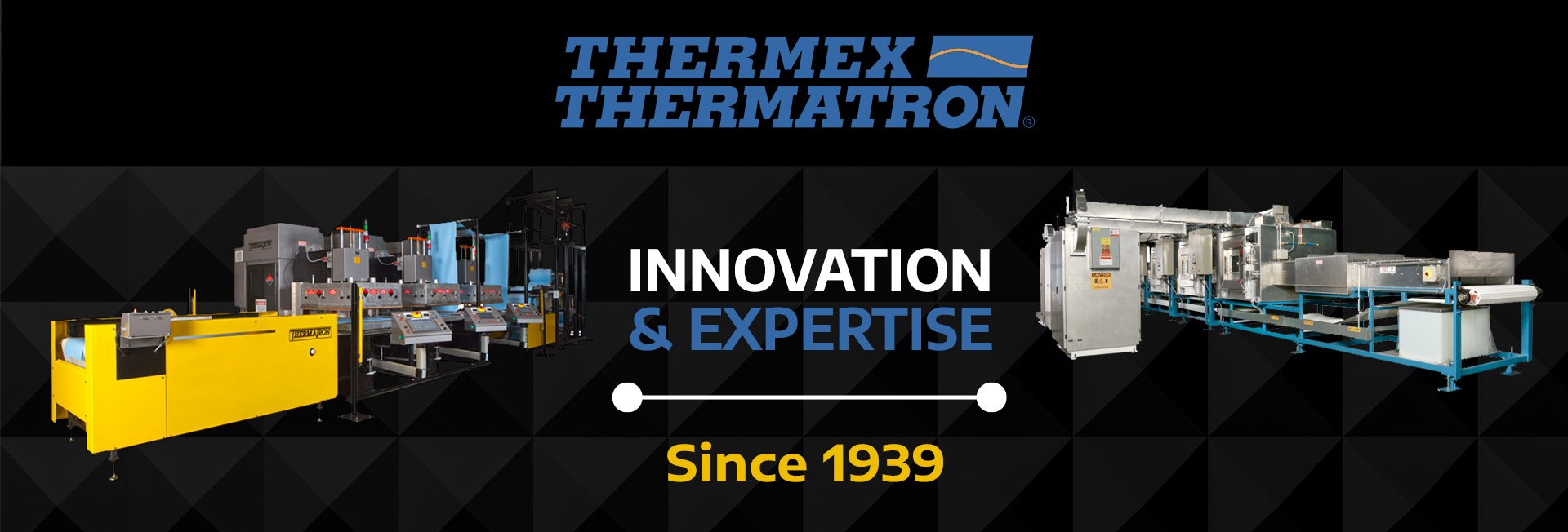