Leveraging Oteman Material Roll Slitting Machines: Consistently Attain Peak Material Production
Thermex-Thermatron Systems
From textile architecture to greenhouses and advertising banners, manufacturers have settled on their expectations for years, finding they would need to wait for materials to be slit to width in apparel as well as industrial and technical fabrics. Utilizing only manual ways to cut materials in the format needed for widespread production can be time-consuming — detrimental to productivity and efficiency.
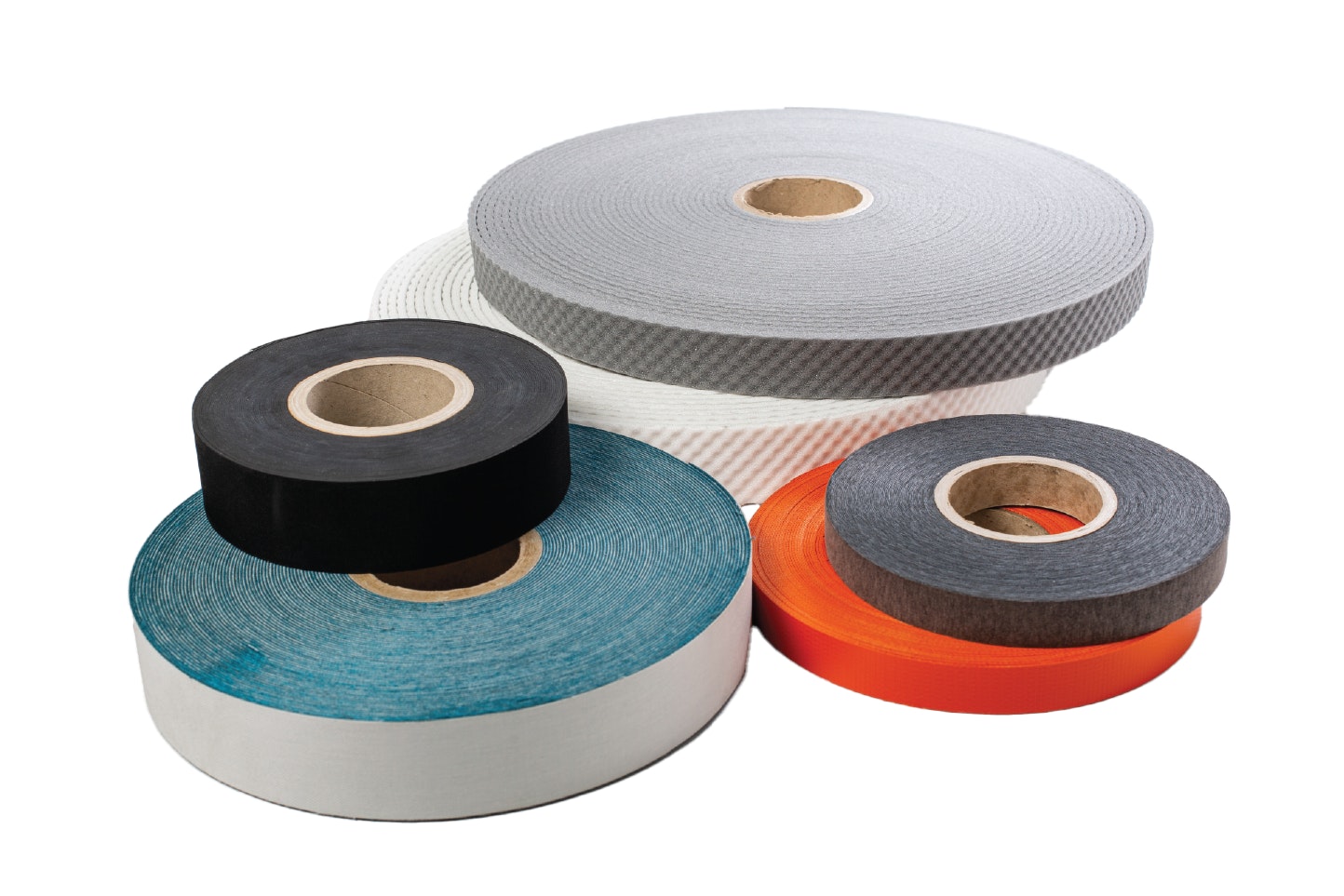
Before the introduction of slitters that could be accurate, automated, and achieve the utmost safety, both precision and accuracy had taken a back seat. This is why Oteman sought to create a family of slitters, now distributed under the umbrella of Thermex-Thermatron Systems (“Thermex”); making state-of-the-art machines accessible in North America. Mining leading technical expertise, pioneering innovative microwave and radio frequency systems that have gone on to shape advancements in every sector from fabrication to adhesives, Thermex has supported manufacturers for over 80 years; fostering safer working conditions, delivering on higher quality with unwavering consistency, and allowing facilities to economize strategic budgets with less expenses.
With Thermex-Thermatron Systems (“Thermex”) as Oteman’s key North American distributor, manufacturers of materials and end products no longer have to contend with crude baloney slicers or manual saws when production calls for slitting material rolls. Enterprises across the country, from conveyor belt manufacturing, textile, and industrial fabric structure manufacturing to plastic, rubber, and vinyl material producers can now leverage Oteman Material Roll Slitting Machines to save considerable money and time; slitting their materials for specialty widths and applications.
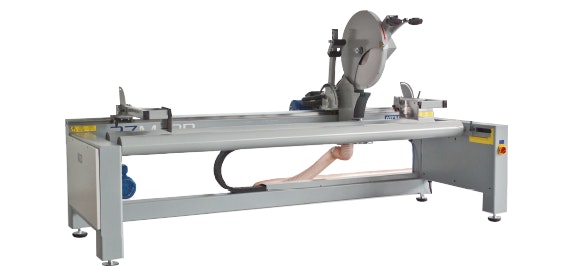
Applying a Highly Engineered Design:
How to Operate Your Oteman Material Roll Slitting Machines
Designed with both manual and programmable options, the Oteman Slitters are available with shaft and non-shaft versions — amplifying flexibility for high production needs. Made to cut rolls of different diameters, weight, and lengths into strips, these slitters extend versatility and drive top performance for multiple roll storage. When manufacturers gain the ability to optimize real-time cutting, yielding the correct width at the essential moment it’s needed, this helps pare down on inventories while facilitating increased deliveries of various materials. Notably, the Oteman Slitter is created to cut a range of materials, including (but not limited to) the following:
- Lycra
- Geotextiles
- Non-wovens
- Synthetic leather
- Rubber
- Fiberglass
- Carpets
- Adhesives
- Fabrics
- PVC, and more.
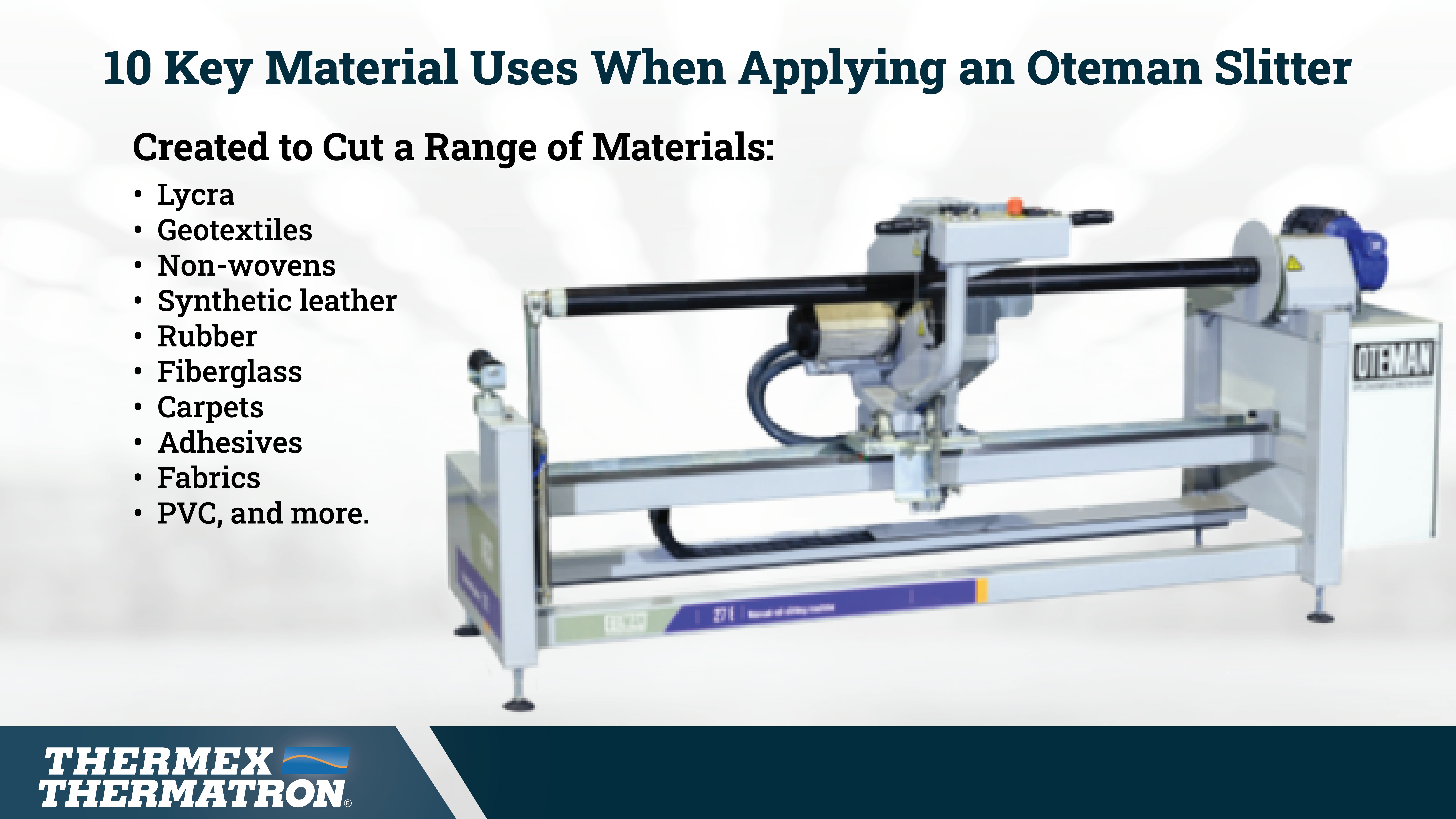
Using multiple tools that alternate with different degrees of bevels, single as well as double, this resourceful system extends to manufacturers three strategic features: self-sharpening, blade cooling, along with a special blade waxing system. Cutting-edge encoders then enable automatic position of the cutting head. Understanding the comprehensive slitting solution industries called for, these slitters were created to integrate variable blade rotation and speed adjustments; and are one of the few slitters that have the capacity to support rolls up to 1700 lbs. along with widths over 10 feet.
Moreover, for jumbo rolls, various loading systems are available with the option to add rewinding systems as part of this adaptable, multifaceted solution. Throughout each functional advantage, the safety of the user remains at the core of this machine’s design. Implementing optional features such as safety light curtains along with special radar sensors help keep operators safe.
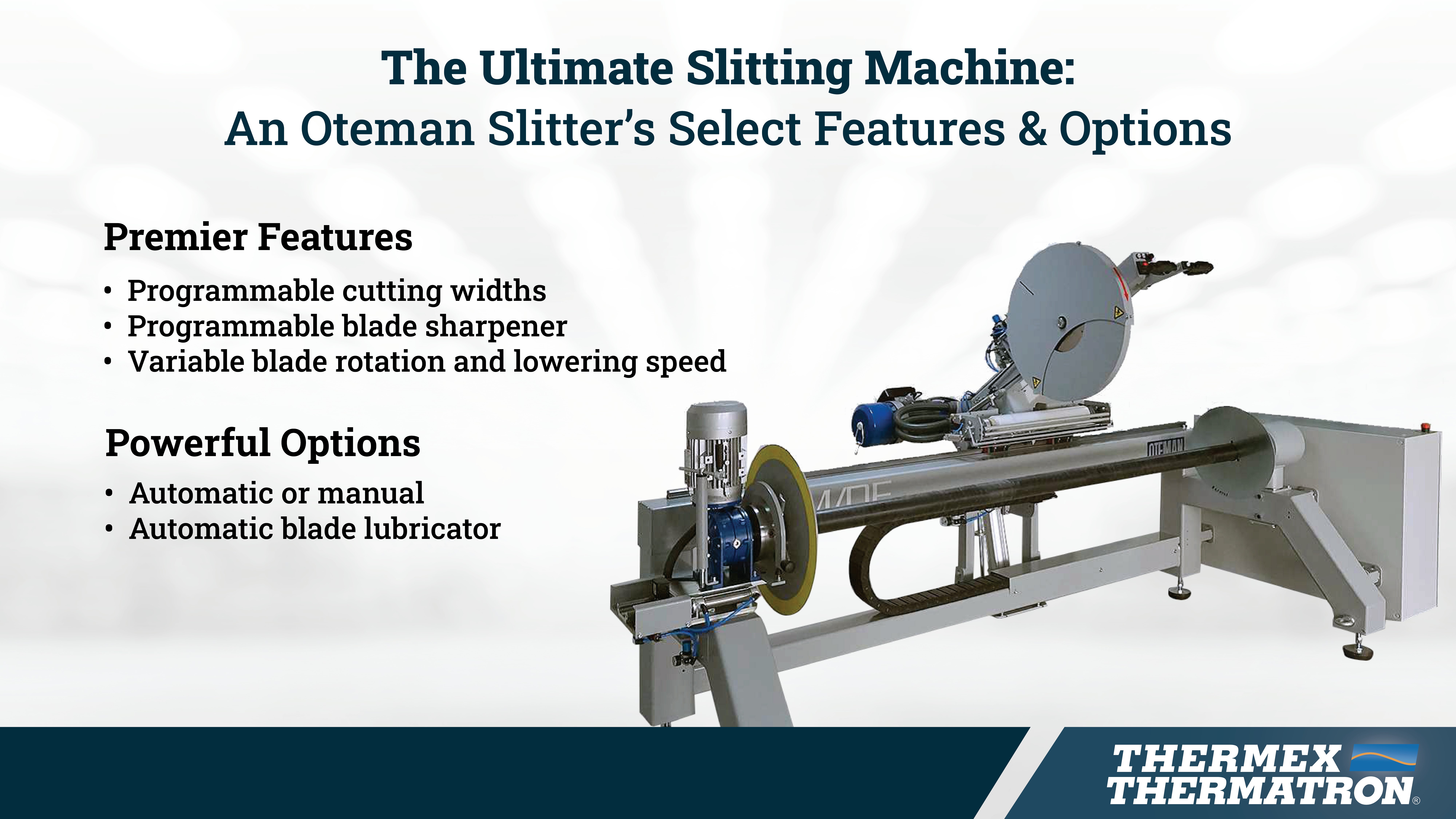
Operating Roll Loading with Your Material Roll Slitting Systems
Before loading a roll, first, you must displace the arm of the machine to a position away from any potential interference. Thermex-Thermatron recommends you leave the machine arm on the side opposite to the roll-dragging motor. A crucial part of the process: bear in mind the material winding direction, as this will determine the roll rotation direction to select.
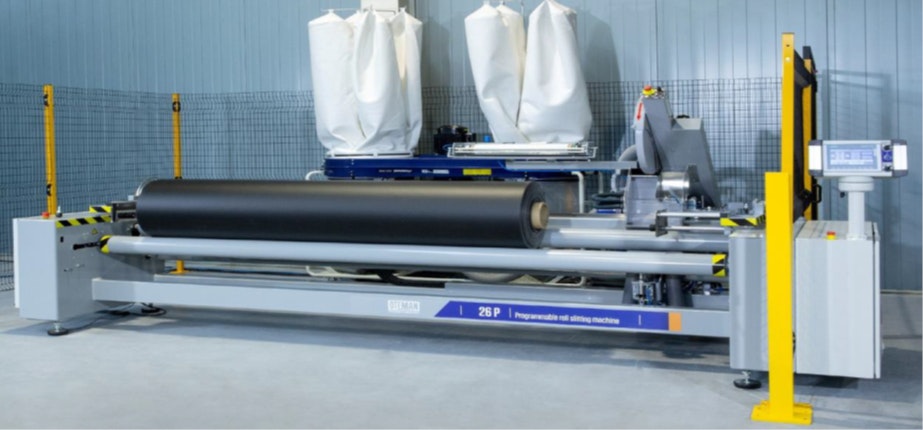
To load the roll into the machine:
- Open the plate protector to prevent from actioning the machine with the key; and then proceed to close the claws using the special tool. While doing so, take care to not press the axis.
- Activate the pneumatic switch to release the axis.
- Open the claws of the plate with the special tool, ensuring that one of the claws remains placed in the lower part of the axis.
- Displace the axis, pivoting it at the end opposite to the plate.
- Load the roll in the axis, using the support of a mechanical device (such as a crane or a pallet jack).
- Next, fit the axis at the center of the plate claws, closing the claws while avoiding pressing the axis. Use this step to guide the entry of the axis into the engine plate joint.
- Place the head in its working position (closed).
- To execute this, first set the pneumatic switch to the right.
- If necessary, raise up the axis, accompanying it, so that you may fit it inside the plate set — and avoid blocking.
- Once the roll is placed in its working position (directly in contact with the plate), remove the mechanical loading device.
- Next, open the plate claws to fix the roll. While doing so, see to it that the roll is not loose, protecting the cardboard tube from deforming. When the anchorage of the roll is finished, the claw key must be withdrawn. Then, you can close the protector of the key. Ensuring that the claws press correctly against the cardboard, you can achieve the last turn with a torque wrench, utilizing a counter-clockwise direction.
- Contingent upon the kind of cut, if required, fit the mobile plate to the other end of the roll.
- The machine is now ready to be rearmed.

Keep in mind, the unload will be the inverse process to the load. Before unloading the roll, you must displace the arm of the machine — once again, away from any potential variables that could disrupt it.
- Open the plate protector and use the special tool to close the claws, making sure to not press the machine’s axis.
- Place the head in its load position (opened). To do so, set the pneumatic switch to the left.
- Open the plate’s claws with the special key, so that one of the claws remains placed in the lower part of the machine’s axis.
- Now you can displace the axis, pivoting it once again towards the end facing opposite to the plate.
- Withdraw the trim or cut bands; and if the weight makes this step of the process necessary, you can do so using a lifting platform.
Gaining an In-Depth Understanding: Maximizing Material Roll Slitting Machines in Application
Trusted to help manufacture bridal fashion, corsetry, as well as swimwear, the Model 27 has the capabilities to lodge rolls up to and including 3.25 m; but can span even further in machines utilizing special measures. This is how the Oteman Slitting Machines are able to navigate a varied range of distinctive, assorted materials; including felts, knitwear, PVC, fabrics, plastic adhesives, cellulose, leatherette, and fiberglass.
Specially engineered, the Model 27 harnesses premier PLC and touchscreen technology, which not only eases and enhances the cutting process; but delivers results at rapid-fire speed, optimizing a 600 mm diameter blade. This machine is set to cut rolls into sections; built with an outside diameter below 500 mm along with an inside diameter larger than 65mm. Developed on standard configurations, Oteman has made it feasible to achieve effortless, and quick maintenance, whenever needed.
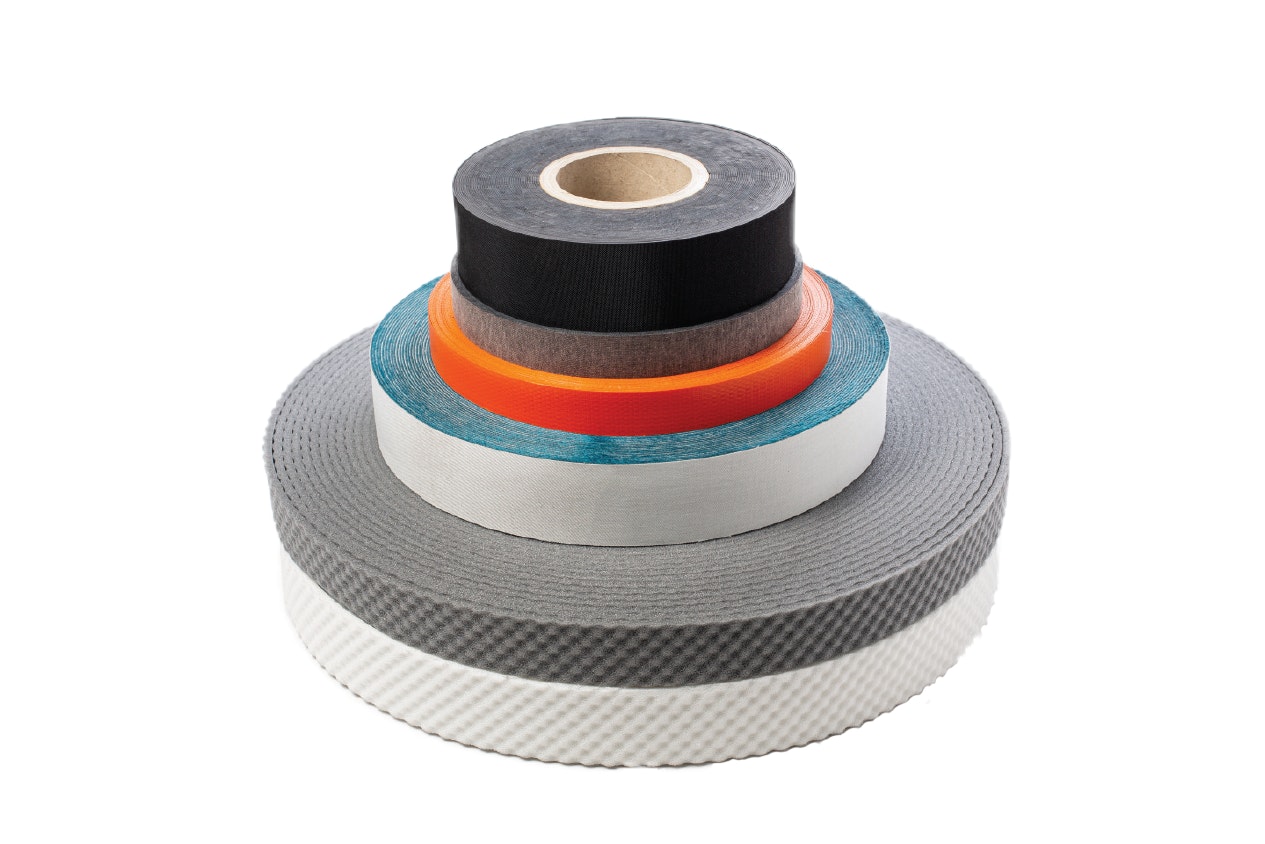
Known for a variety of names, roll slitters are also referred to as:
- Log slitters
- Baloney slicers
- Baloney cutters
- Single knife roll slitters
- Roll cutters
Notably, baloney or log slitters are similar to deli slitters. Using a large circular blade or fixed band blade, roll slitters wield the power to cut all the way through a dense roll of material. This machine is so effective, it is capable of cutting down through the very core that wound the material.
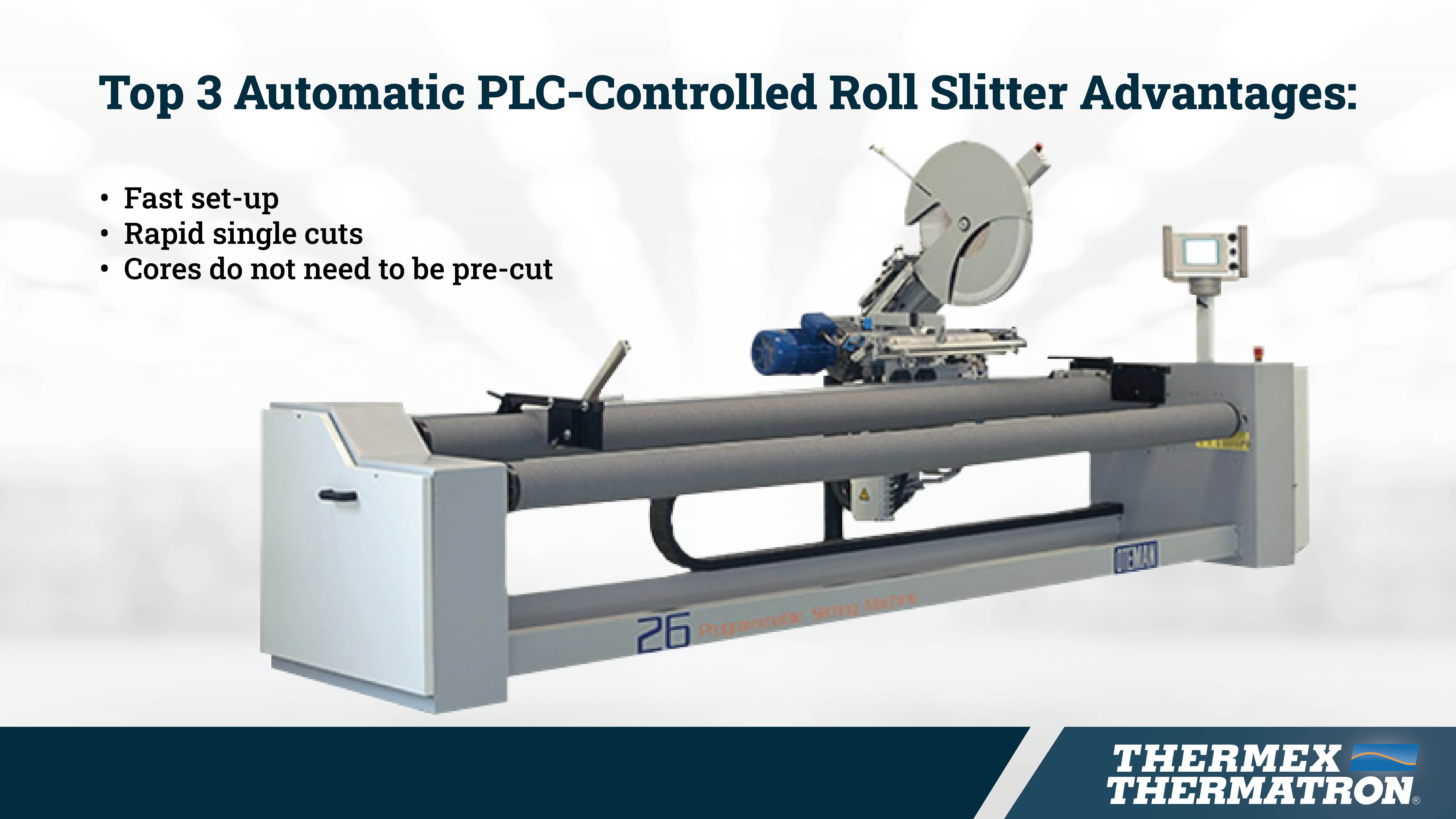
Once materials are slit, customers may use these spare resources for the following:
- The belting industry may leverage the cut materials in conveyor belts, sidewalls, and cleats.
- The textile industry can take these cut materials and convert them into clothing, awning, tents, tarps, carpets, and rugs.
- The plastic / rubber / vinyl industry is able to take these finished materials and bolster barriers, linings, tents, domes, and pipes.
- The building industry can explore the possibility of slitting insulation for PVC pipes and other flexible materials.
Discover the Labor-Saving Impact of Highly Engineered Systems: Made for Optimal Versatility
A standard Oteman Slitter, with approximately 15 feet (4.8 m) in width and scaling at around 6 feet (2 m) height, can be programmable for higher volume slitting; or can offer a manual model for lower volume. To determine the best slitter for the job at task, it comes down to the weight of your materials. For lighter weight materials, an Oteman Slitter with a shaft offers the precision to smoothly protect top outturn; whereas for heavier rolls, an Oteman Slitter without a shaft is the best possible resource. This allows users to slit all ranges of different materials in pivotal industries from aerospace to medical to arenas that shape our daily lives; including carpet manufacturing, rubber products, conveyor belts, and industrial filters.
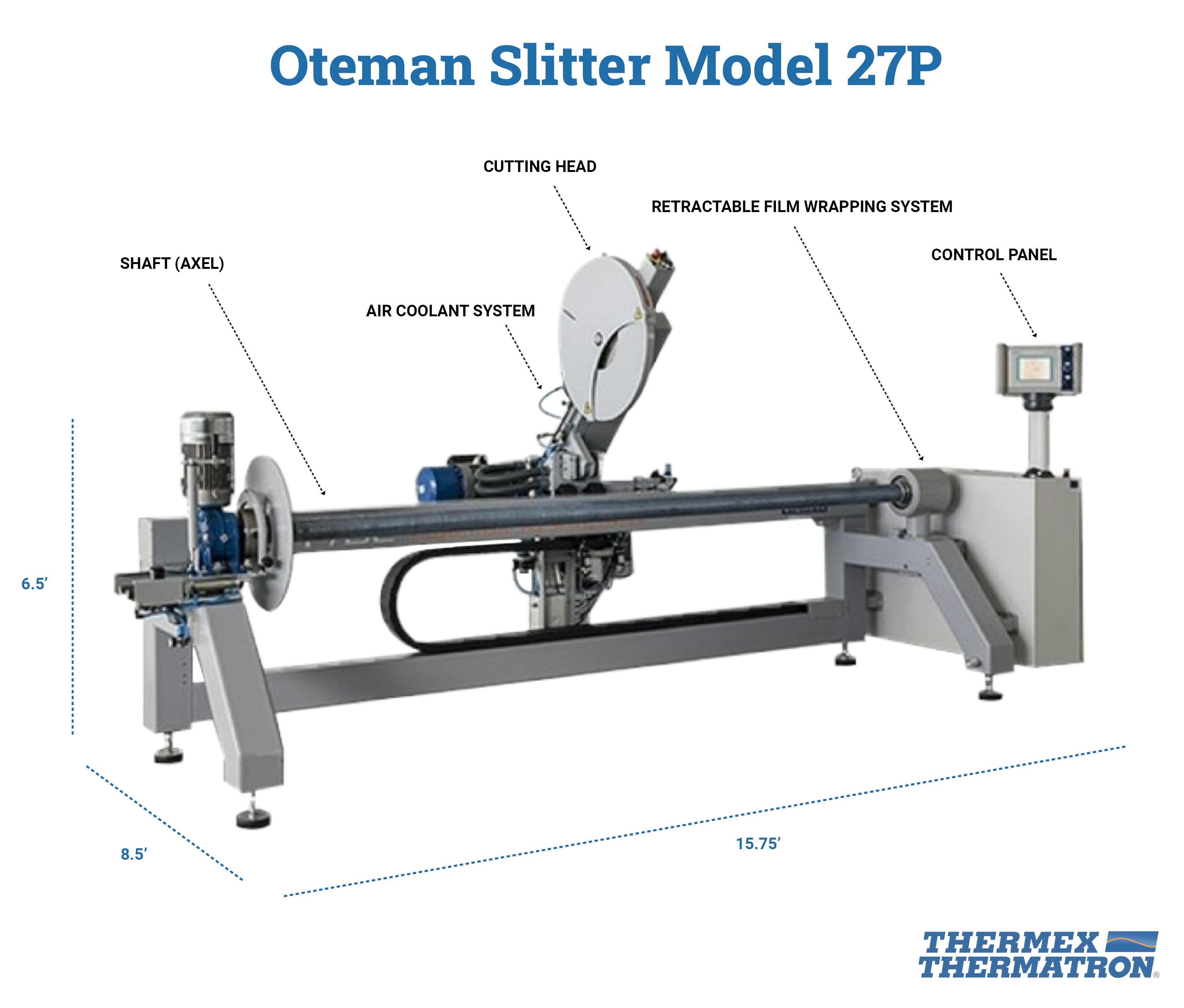
These slitters have the power and agility to slit through apparel as well as industrial and technical fabrics, adapting to materials and sectors across-the-board. From truck awnings to high-speed doors and geomembranes, a modular build and tremendous flexibility allow these highly advanced machines to specialize in cutting even the most complex fabrics; including silk, tulle, crepe, and chiffon.
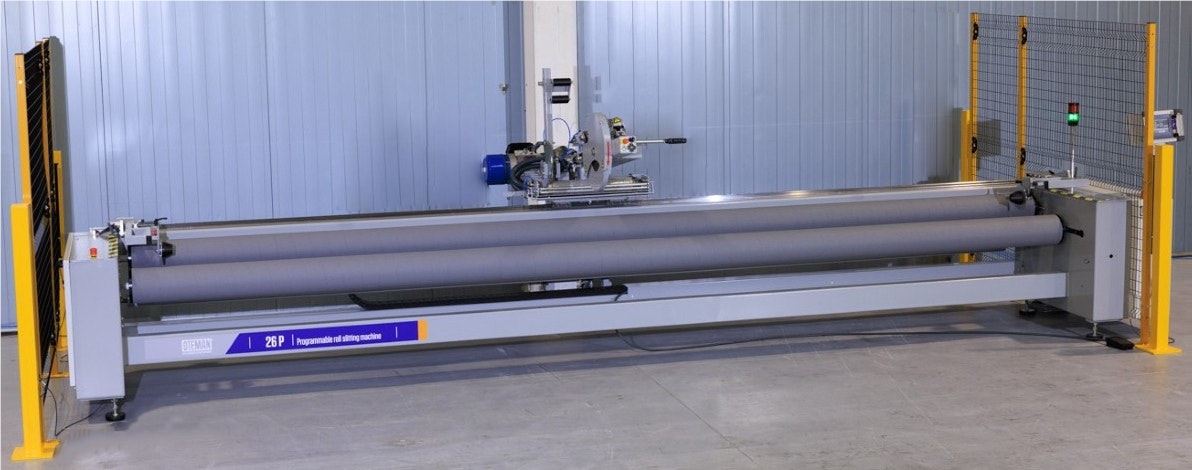
The Leading Benefits of Utilizing an Oteman Slitter
- Manufacturers can bring the slitting of bulk rolls in-house, where the slitting is fulfilled to order in a real-time scenario.
- This allows for a variety of different cuts to be achieved whenever needed.
- The confidence of producing in-house allows for elevated quality.
- Companies are able to incorporate these slitters directly into their manufacturing processes — without depending on outside sources or waiting periods.
- Oteman Slitters are extremely accurate — precision down to within a single millimeter.
- A small percentage of companies are able to leverage the ability to provide industrial slitters, using a program that guides the gantry via heavy duty motor to drive their systems.
- Because they are built sturdy, this level of endurance and durability allows Oteman slitters to accommodate the widest material rolls in the industry.
- Powerfully engineered, these machines are ready and able to slit a high variety of materials, benefiting an extensive array of industries, each with unique needs.
- When wrapped and condensed, even insulation can be slit with these effective tools.

With some slitters, sticky material can cause abrasion or friction, where the slitting process could cause it to stick further as it heats up the material. Using the wrong tools can cause undue heat to the material. The Oteman slitting advantage: these machines do not require the material to be unwound. This means sticky material will not pose potential issues, because there is no undue heat added to the slitting process (a rapid-fire technique sometimes referred to as “saw it off the log”).
If the material is not too sticky or heavy, roll slitters offer the perfect design to deliver overall accuracy. When navigating a program that utilizes recalled settings, a programmable version is the ideal option. Additionally, the manual version is highly functional, ready to service an extensive selection of materials.
Serving as Oteman’s sole North American distributor, Thermex-Thermatron has been engineering crucial resources for manufacturers since 1939; harnessing critical research and real-world insights to develop the resources production facilities need to drive valuable, consistent, and refined outcomes. The Oteman Slitting and Cutting solutions are just another example of productivity improvement tools available within the growing Thermex-Thermatron equipment product line, in addition to its full line of high frequency welders, industrial microwave systems, industrial radio frequency systems, and industrial press systems.
For more information, visit our website at thermex-thermatron.com.
For FIAB and Oteman inquiries, contact our Director of Business Development, Traci Evling (Traci@thermex-thermatron.com; 502/916-8981 or 904/662-2169).
For Thermex and Thermatron inquiries, contact our Director of Sales, Dean Mancuso (Sales@thermex-thermatron.com; 502/916-8972 or 502/243-5636).