Not All Thermoplastic Materials Are Meant for Welding: Here’s What You Need to Know About Thermoplastics
Thermex-Thermatron Systems
Serving the Industrial Radio Frequency (RF) and Microwave (MW) industries, Thermex-Thermatron Systems (“Thermex”) has applied over 80 years of optimized innovation and leading expertise to each product, helping manufacturers leverage crucial heating technologies. Highly engineered RF Preheater Systems accelerate enhanced production, improving precision and sharpening material performance. Developing a key understanding of how to best harness RF heating will allow you to reap the full benefits of thermoset plastics on the production floor.
What Makes a Material Thermoplastic?
Any plastic materials that gain pliability through the process of heating, able to be bent when the heat reaches a certain temperature, then proceeding to cool and harden, are deemed thermoplastic. Consider that thermoplastic welding signifies the process of joining together thermoplastic material pieces through a three-pronged combination: heating, pressure, and cooling. First, to weld, you should heat the surface of your thermoplastic material until you achieve its melting point. There, it can enter a thermoplastic state. Every material’s thermoplastic state is unique, often ranging between 220 degrees F (105 degrees C) and 380 degrees F (193 degrees C). Next, you should press the material together, allowing it to cool, so that the pressure of the molecules within the material have the opportunity to bond with the other piece’s individual molecules.
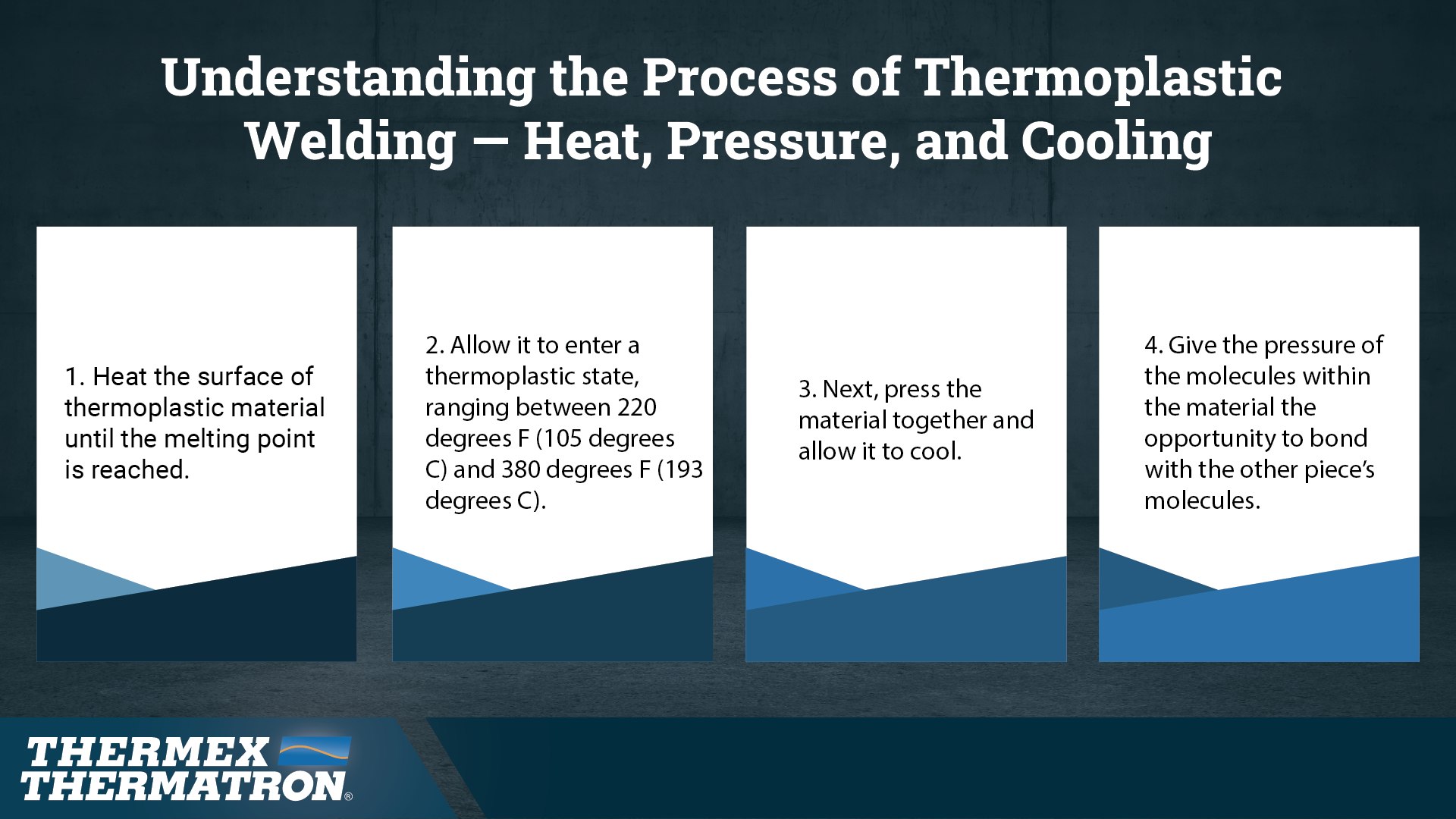
The Benefits of Utilizing Thermoplastics in Manufacturing
Manufacturers often turn to thermoplastic materials throughout the industry, taking advantage of a multitude of applications. In fact, many of the consumer goods we use were made using thermoplastics, along with thermoplastics that yield essential medical equipment, sturdy packaging, reliable storage, as well as critical machine parts. The value of using thermoplastic materials is enormous.
The top five reasons thermoplastic materials have become popular among manufacturers include:
- Lightweight materials are easier to manufacture.
- High strength makes thermoplastics an asset for delivering accurate, measured results.
- Greater design flexibility, which makes the materials adaptive to user needs.
- Economic advantages from processing cost savings because the materials are far more cost-efficient.
- Significantly less corrosive and stronger fatigue properties compared to metals.
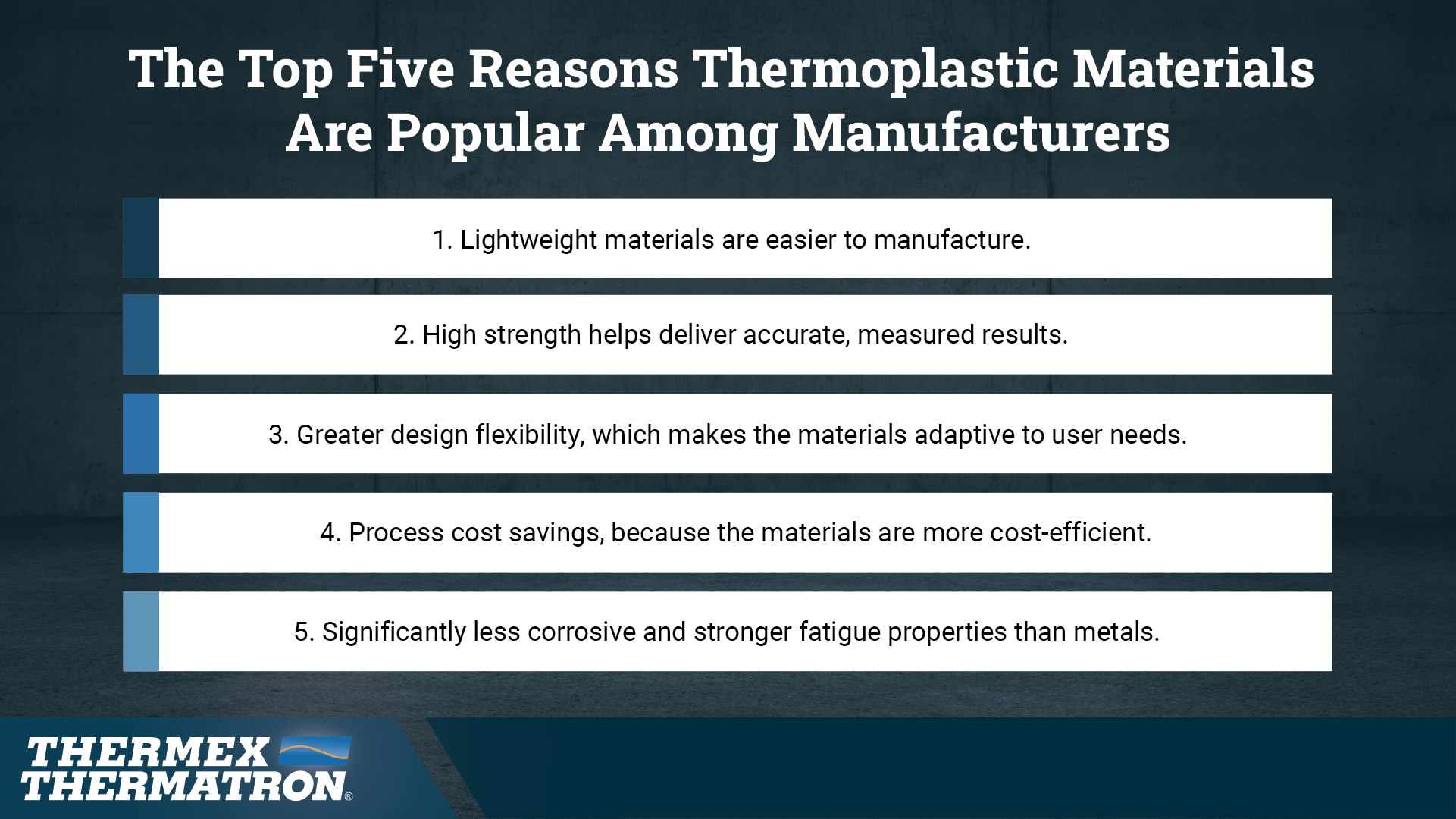
Learn Which Thermoplastic Materials Are Made for Welding
While welders often turn to thermoplastics, not every thermoplastic material is able to be welded. Discover some of the most commonly welded thermoplastics along with their prime applications:
- Polypropylene (PP): Throughout a breadth of applications, ducting and packaging industries frequently turn to polypropylene coated fabrics, harnessing its strength in products such as reusable plastic containers or car batteries. Additionally, polypropylene coated fabrics offer medicinal properties, used in hernia repairs as well as creating heat-resistant medical equipment.
- Polyethylene (PE): Across the years, the agriculture and geomembrane trades have welded polyethylene, and now, the sign industry has joined in on leveraging this thermoplastic’s incredible properties. Many strains of polyethylene are classified through the lens of structure, whether density or molecular; and each one offers unique application advantages. The four most notable include:
a. Ultra-high molecular weight polyethylene (UHMWPE)
b. High-density polyethylene (HDPE)
c. Medium-density polyethylene (MDPE)
d. Low-density polyethylene (LDPE) - Polyvinyl Chloride (PVC): A must-have for the sign, ducting, tent, banner, and awning sectors, these industries flock to using polyvinyl chloride laminated fabric. Tough, and yet simultaneously lightweight in nature, this thermoplastic material is advantageously resistant to bases and acids alike. Moreover, those in construction also reap PVC’s benefits, using it for roofing sheets, gutters, drainpipes, as well as in vinyl siding. Immensely flexible, PVC can be converted into tubing, hoses, waterbeds, electrical insulation, and upholstery.
- Polystyrene (PS): A multi-form asset, similar to PVC, manufacturers utilize polystyrene for applications across-the-board. For instance, find extruded polystyrene (PS) in CD and DVD cases, disposable cutlery, plastic cars and boats, along with smoke detectors. Behind the foam peanuts that help when packing fragile materials, manufacturers are using expanded polystyrene (EPS). Extruded Polystyrene foam (XPS), which the public most commonly sees as Styrofoam, is multi-purposeful, used to create architectural models as well as beverage cups.
- Acrylic: A shorter name for polymer poly methyl methacrylate (PMMA), acrylic is also referred to as Lucite, Plexiglass, and Perspex. It’s the leading glass substitute, seen in automobile lights, aquariums, submersible viewing points, as well as in aircraft windows. Moreover, manufacturers rely on acrylic to build signs, from the lettering to the logos. The medical sphere finds acrylic useful, a powerful replacement for eye lenses and also used in bone cement. Often heat-resistant, the only way to weld acrylic is through a medium like thermoplastic seaming tape.
- Nylon: Part of polyamides, a class of polymers, nylon offers a silk substitute for various products, from women’s stockings to parachutes. In bulk form, nylon lends itself for use in mechanical parts, including machine screws, power tool casings, along with gear wheels. Many times, you can find nylon fibers in musical instrument strings, rope, carpets, and assorted fabrics.
- Teflon: This thermoplastic is best-known by the name, “Teflon,” a brand that DuPont Corporation devised to label the non-stick coating on cookware. Likewise called polytetrafluoroethylene (PTFE), because it is a polymer, this gives the thermoplastic chemically inert properties; a benefit for making containers and pips that must confront reactive chemicals. Therefore, Teflon is additionally utilized as a lubricant in sliding parts, serving to lessen the wear that results from friction. Notably, only a select type of high heat and cooling systems can be used for welding Teflon.
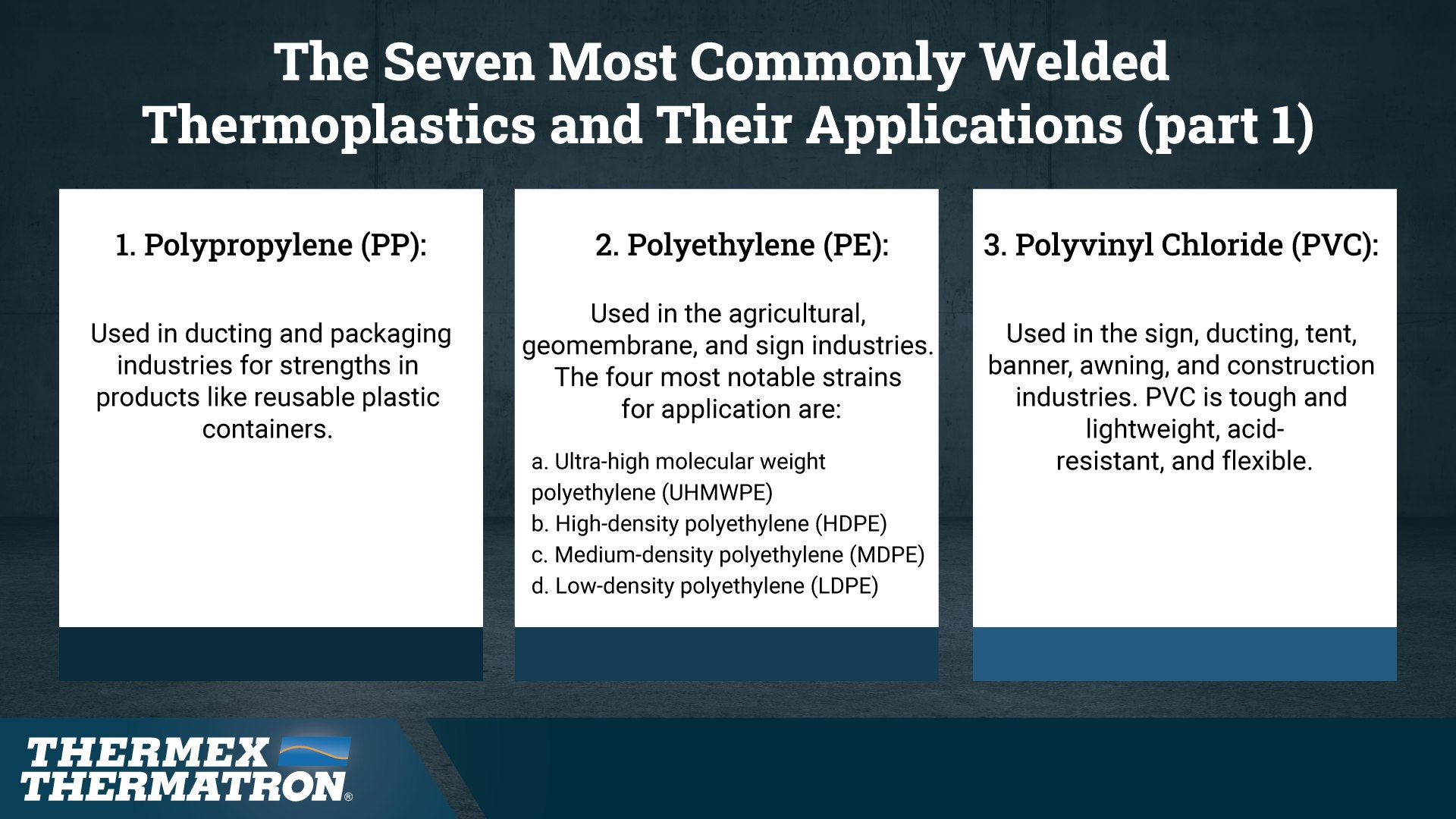
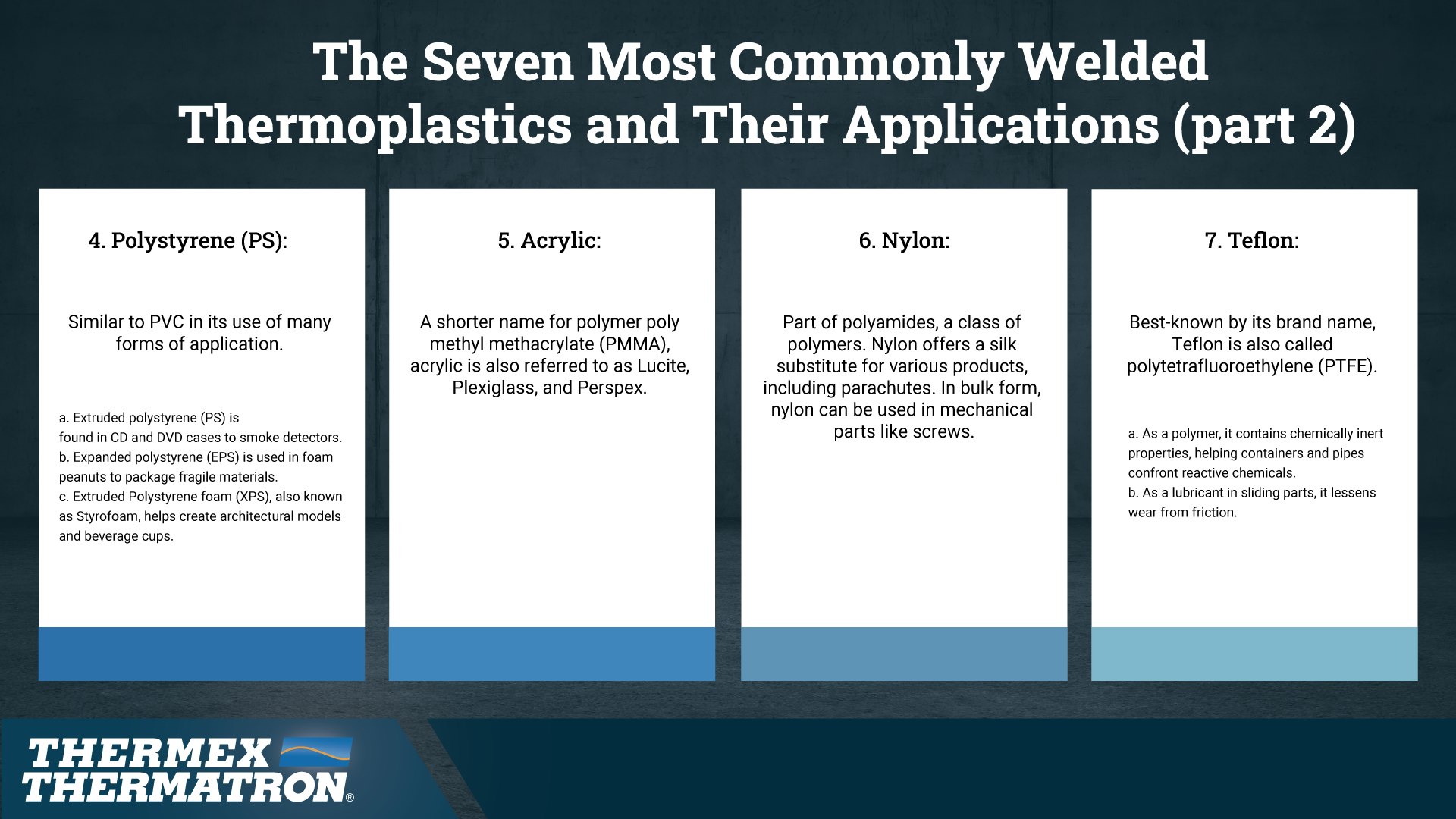
Most of these thermoplastic materials serve in Ultrasonic or RF welding. Along with them, additional materials like Open Celled Polyurethanes, PET, PETG, PEVA, LDPE/EVA, as well as certain ABS plastics may also be appropriate for welding. On top of these thermoplastics offering a larger slew of weldable materials, manufacturers benefit from other advantages that come with RF welding, such as:
- A reduction in set time
- Zero toxic adhesives
- A strong seal that is airtight
- More even distribution of stress
- A seal that is tighter, protecting thicker materials
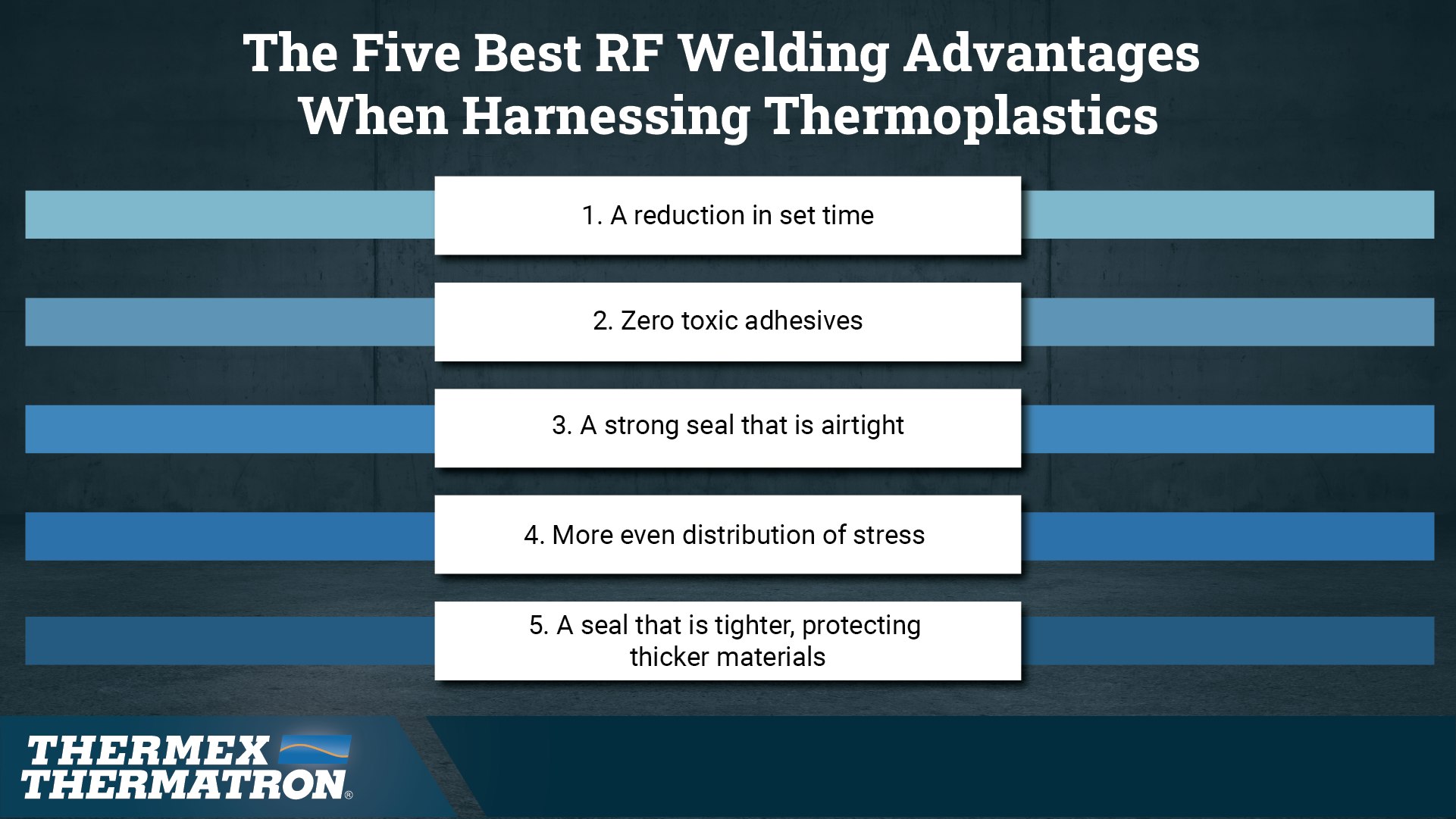
Moreover, considering welders produce heat solely at the weld spot, these materials mean the piece will not be impacted by heat-degradation. If you are noticing less efficiency with the machine you are using, you may find that your current welder is failing to deliver the impact you need for the task at hand. Trusted for robust durability and engineering efficiency, Thermex-Thermatron provides RF Welders and RF Heat Sealers that equip you with valuable output power capabilities, ranging from 1.2kW to 40kW. These RF welders can be utilized to weld or fuse thermoplastic materials, including PVC, polyurethane, PET, among others.
Our high-quality industrial RF Welding Systems are made for producing a long-lasting, solid, and even seal on all kinds of materials. Whether you’re using thermoplastic materials to create packaging, medical, fabric, or automotive products, we’ll tailor our customized RF Sealing equipment to the specific requirements of your industry’s sealing and heating processes; designed to deliver you the ultimate effectiveness for your operations; so, you can maximize the pivotal benefits of thermoplastics.
For Thermex and Thermatron inquiries, contact our Director of Sales, Dean Mancuso (Sales@thermex-thermatron.com; 502/916-8972 or 502/243-5636).
For FIAB and Oteman inquiries, contact our Director of Business Development, Traci Evling (Traci@thermex-thermatron.com; 502/916-8981 or 904/662-2169).