Maximizing The Science of Process Heating Through RF and MW Technologies
Thermex-Thermatron Systems
A leader in the industrial microwave industry for over eight decades, Thermex-Thermatron’s technology has been used in applications across the globe: from the automotive sector to medical, aerospace, composites, and food processing. The science of process heating is multi-faceted and far-reaching, affecting the way we interact with the world around us — and its core has always been one of process control. The ability to precisely control each variable is the cornerstone of this science, determining the duration of heating and how that heat is applied to materials. Radio Frequency and Microwave Industrial Heating have become increasingly valuable: two proven technologies with the power to significantly improve process control. Using the most reliable technology will help you better leverage the science of process heating.
UNDERSTANDING THE BASICS OF MICROWAVE PROCESS HEATING
From the outside in — this is often the most common way we tend to heat a product. Heat penetrates into the interior of a product, molecule by molecule. As a general rule, when a product’s moisture content is high (50 to 95%), conventional heating methods like convection (hot air) and infrared are considered the most economical technology. However, when it comes to heating products with low moisture content (20% or below), innovative technology is needed.
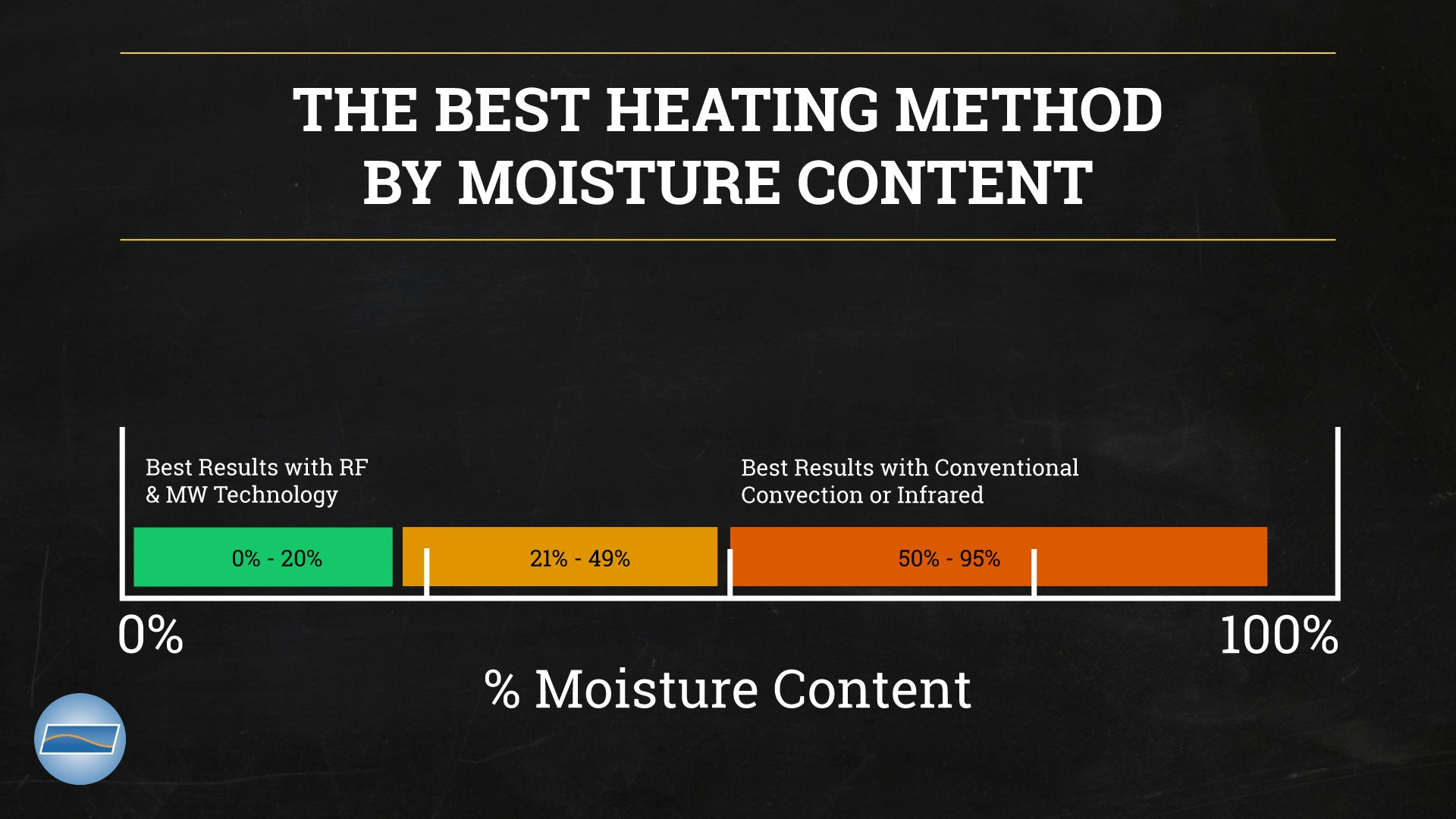
Microwave energy carries the unique ability to heat certain molecules while not heating others, allowing process heating to be more exact. Manufacturers often utilize microwave energy for this reason, drawing out the last few percent of moisture in a range of products. That greater level of precision can be especially helpful in applications such as dry chemical processing, where any moisture not removed could pose damaging results. Another key advantage of the microwave process: it can be completed quickly without overheating the already dried material. Moreover, with microwaves, materials can be dried to levels as low as 3% moisture content within a relatively short time.
Similar to light through glass, microwaves can also pass through a product. Yet, plastics, for instance, would not react to those waves, because some materials do not contain a dipolar electrical charge. However, a material like water reacts differently, considered the most common substance with a dipolar charge. Unlike plastic, asymmetrically charged materials react to microwaves by trying to align themselves to the electromagnetic field. The electromagnetic field’s capacity to change polarity is rapid; as much as a couple of billion times per second. Likewise, dipolar molecules continually change alignment, producing energy that is converted into heat. Water molecules proceed to heat themselves until the product becomes so hot, the water evaporates.
WHEN AND HOW TO USE MICROWAVE HEATING METHODS TO YIELD POWERFUL RESULTS
In many applications on the production floor, a hybrid combination is often the most impactful: using microwave technology along with conventional heating methods. Whether before, during, and/or after the microwave stage, knowing when to use conductive or convective processing steps depends on both product and process.
For instance, if you use microwaves first, the results yield more effective initial heating. However, if you apply conventional and microwave heating at the same time, you’ll achieve a synergistic effect. Microwave heat will pump the product’s moisture to the surface, producing better drying results than convection-only systems. One example of this is drying vegetables:
Combining convection and microwave zones in a vegetable dryer reduces processing time, thereby speeding production. Using a combination approach, vegetables with 90% moisture content can be processed in the convection zone for two hours, followed by microwaves for 15 minutes. Final drying is completed in another hot-air convection zone for 15 minutes. With some vegetables, final pasteurization can be incorporated into the finish drying. By using an oven with a microwave zone, you can trim more than eight hours of through drying as well as another eight hours of final bin drying from the production cycle.
For many products, using a microwave zone near the end of the process, with or without hot air convection, produces the best results. Yet, with conduction only, once the product’s moisture content drops below 25%, there becomes a danger of overheating the product’s surface, which causes a “skin” to form. To prevent this, it’s crucial to allow the product to rest, or equilibrate, while the water vapor works itself out of the product. Otherwise, if you were to use continuous airflow, the product’s exterior could over-dry.
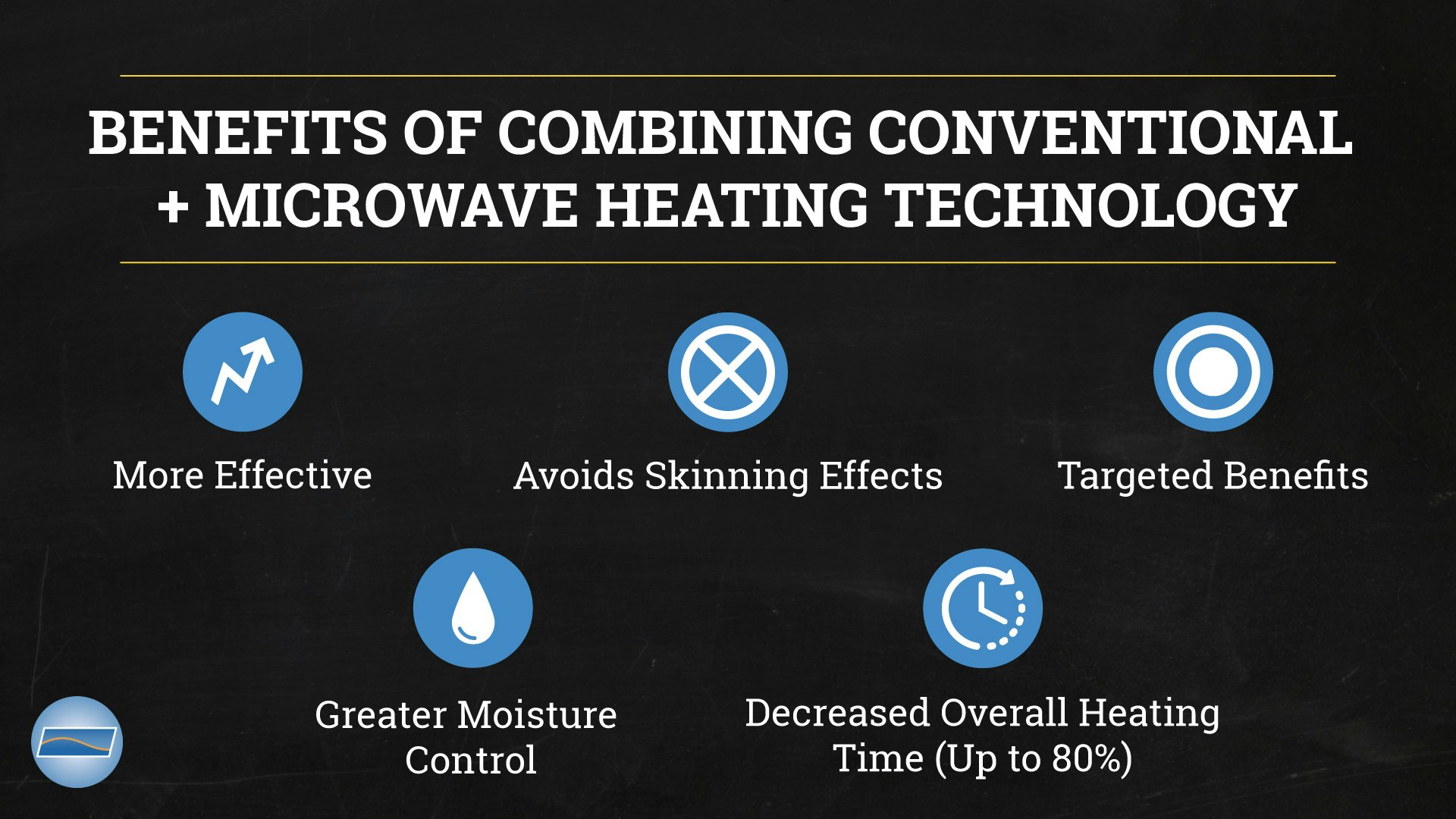
This is why combining the two methods of heating and drying (convection and microwave) is so advantageous: it avoids the skinning effect while also providing quick processing. In the first stage, using convection heat allows a large percentage of the moisture content to be quickly removed. Because the moisture is high, equilibration periods are not required, and yet, the product’s exterior does not skin over either. Once the moisture content level drops below 24%, the product can convey into a microwave zone. Wherever the moisture remains deep in the product’s interior, it is quickly driven to the product’s surface. This synergistic combination of heating methods can cut overall heating time by up to 80%.
TOP 7 WAYS TO OPTIMIZE MICROWAVES IN INDUSTRIAL PROCESSING
Whether used in combination with conventional heating or alone, microwaves play a key role in enhancing industrial processing. Here are the seven leading ways that applications of microwaves can transform industrial processing results:
- Baking
The ability of microwaves to speed internal heating can accelerate the baking process. Microwave heating can be combined with convection or infrared heating to create a crispy crust in foods — providing an aesthetically pleasing appearance in much less time. - Blanching
When combined with a humid or steam atmosphere, rapid uniform heating with microwaves can be effective for blanching fruits and vegetables. Moreover, microwave processing won’t incur the leaching losses associated with hot water or steam blanching. - Curing
Because it leads to rapid heating throughout the product, microwaves may be used for bulk polymerization reactions that are heat initiated. - Disinfestation
Destruction of larvae and insects in dried foods using microwaves is not only an economic solution, but an efficient one. - Moisture Leveling
The heating effect of microwaves is roughly proportional to their moisture content. This means microwaves can be used to equalize the moisture content within a product that has a non-uniform moisture level. - Removing Solvent
Many solvents are efficiently vaporized with microwaves, which permits solvent removal at relatively low temperatures. Microwaves can also be used to cure glue and other adhesives. - Tempering
Microwave systems are widely used for tempering deep frozen foods, including beef, pork, poultry, and seafood. Using microwave technology trims the thawing process to a matter of minutes. This likewise helps to keep the integrity of the product intact.

THE IMPORTANCE OF USING QUALITY RF AND MW INDUSTRIAL HEATING EQUIPMENT FOR PROCESS HEATING
Through the introduction of process integral derivative (PID) controllers, PLCs, and computers, the advent of digital technology has revolutionized temperature control. Likewise, the introduction of infrared heating in the 1930s transformed process heating. However, for most processes, little has changed in the source or application of heat since then.
This is why Radio Frequency and Microwave Industrial Heating are such compelling technologies. The same PLC and computer technology that improves traditional heating methods achieves a rare synergy with RF and MW heating — unparalleled in speed, versatility, and precision.
Part of what makes Radio Frequency and Microwave heating technologies so unique is the way they help develop the heat: within the product itself. This allows for more uniform heating at an accelerated rate. Heat can then be applied deep within a mass without having to wait for the heat to “soak” through.
Radio Frequency and Microwave industrial heating systems have inherently low thermal inertia. This means many materials can be processed in an environment that is essentially ambient. In these applications, the energy input to the product can be modulated in real time, offering near instantaneous process control.
Radio Frequency and Microwave heating are also used in conjunction with conventional heating methods like convection. The reciprocal effect of combining Radio Frequency or Microwave technology with conventional heat produces results that are impossible to obtain with other methods. For instance, the synergy makes it feasible for a product with a large cross section to be heated uniformly, from surface to center. This is especially useful for materials like ceramics, which shrink when dried. Moreover, uniform drying alleviates the cracking that occurs when the outer surface dries, shrinking before the center.
Radio Frequency heating and Microwave heating are clean heat technologies. When using them, you will not risk introducing any combustion contaminants to either the process or the environment. Among many advantages, these technologies are especially well-suited for drying applications. Because of the high susceptibility of water to Radio Frequency and/or Microwave energy, this allows the drying process to be self-equalizing. Areas of high moisture content will then draw more power than dryer areas. This is extremely beneficial for moisture leveling. Additionally, this kind of drying process serves well the conditioning of grains, wood, and forest products, as well as foods like cookies and crackers.
ASSESSING AND CHOOSING THE BEST MW TECHNOLOGY FOR YOUR PROCESSES
Microwaves react with products very differently from conventional heating methods. Therefore, having the opportunity to test your product with microwaves will be instrumental to your production success. When evaluating how suitable Radio Frequency or Microwave industrial heating equipment is for a particular application, it is necessary to consider three key factors: the goal, the materials, and the process requirements.
Consider that the right technology mismatched in an ill-suited application will not yield the results you want. To ensure the best technology can be correctly applied, first you should submit materials for testing. Additionally, the applications laboratory should be equipped to test both RF and MW technologies.
Thermex-Thermatron’s in-house laboratory — ThermaLab — is a facility designed for this pivotal testing. In fact, ThermaLab holds a number of dielectric heating systems, including a 100kW Microwave system that can be used for both conveyorized and batch processes. For over 80 years, we have developed, built, and manufactured high-power industrial systems; technology that has helped make work conditions safer and more efficient throughout the industry.
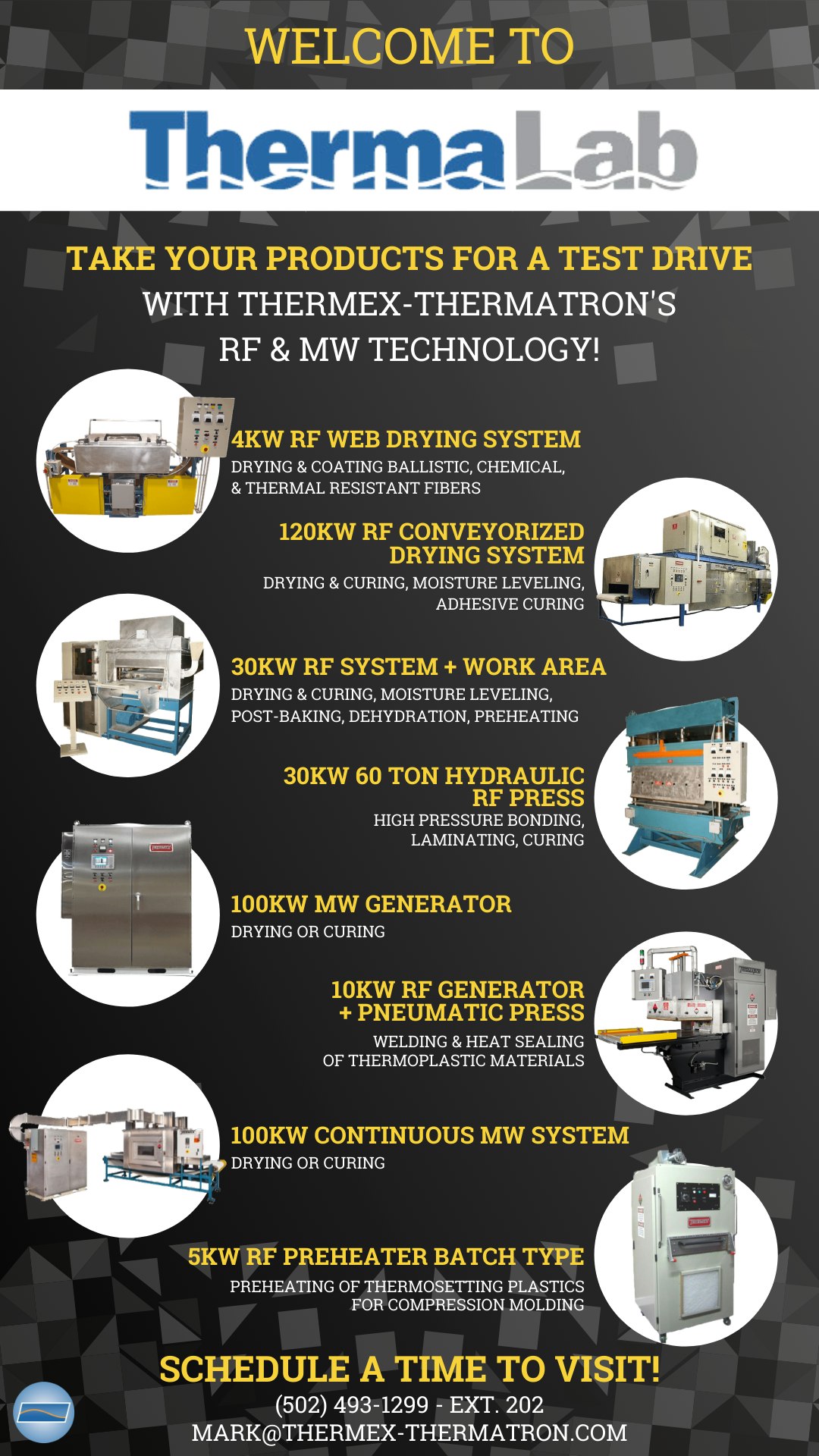
For Thermex and Thermatron inquiries, contact our Director of Sales, Dean Mancuso (Sales@thermex-thermatron.com; 502/916-8972 or 502/243-5636).
For FIAB and Oteman inquiries, contact our Director of Business Development, Traci Evling (Traci@thermex-thermatron.com; 502/916-8981 or 904/662-2169).